Hard Chrome Plating Training Course
Section 2—Introduction to Hard Chrome Plating
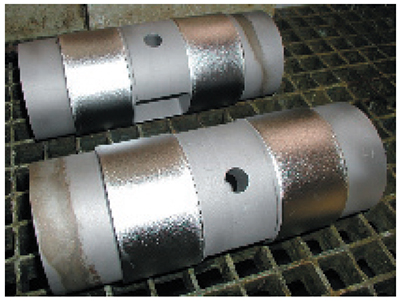
Exhibit 2-1. Each of these aircraft parts has two regions plated.
Hard chrome plating is a remarkable process. Take something made of soft steel, and polish it up a bit. Now scrape it with a file. Notice how easily the file cuts the steel? Now plate it with a hard chrome coating – we'll see how that's done in a minute. Remove the part from the plating tank, and rinse it thoroughly in the rinse tanks. Notice anything different? It's a different color now – a rich, lustrous, bluishsilver color. Grab that file, and try to scratch the part again. What a difference! This time the file glides effortlessly over the chrome plated surface, without removing any metal at all. The plated part is now harder than the file!
What does it take to apply this extraordinary coating? Here is the process in a nutshell: first clean the part thoroughly, and then immerse it in a tank filled with warm chromic acid. Attach it to the negative terminal of a direct current power supply. Put some lead anodes into the tank, and connect them to the positive terminal. We're using a special power supply, a plating rectifier – it's got a switch on it that allows you to reverse the positive and negative polarity temporarily. Set the switch so that the current is reversed, and turn on the power – this reverse current phase will take about a minute. Now reset the switch to forward current, and wait an hour or two. Now turn off the rectifier and pull the plated part out of the tank.
That's it. No high temperatures, bright flashes, or loud noises. It's all done with a combination of chemistry and electricity.
That's why chromium plating is called an "electrochemical" process. The chromic acid solution in the plating tank supplies the chromium metal, but that isn't enough. Directcurrent electricity is also needed. That's what converts the chromium ions in the bath to atoms of metallic chromium on the surface of the steel part. The thickness of the chrome layer increases each minute that the part is subjected to the surrounding chemicals and electric current. We'll be discussing the process in more detail later in the course.
Hard Chrome vs. Decorative Chrome
There are actually two main types of chromium plating, generally called "hard chrome" and "decorative chrome." The differences between the two processes are highlighted in Exhibit 2-2.
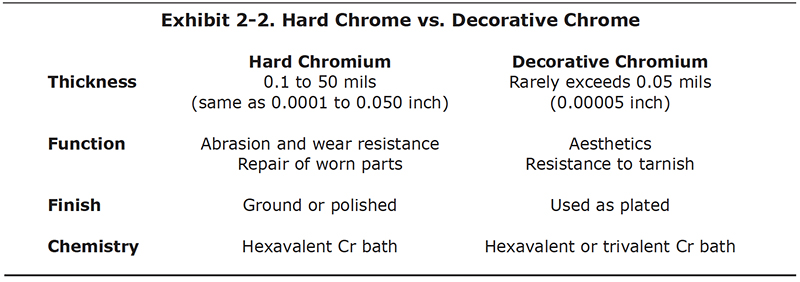
Hard chrome plating, used for functional purposes like wear resistance, is the main topic of this course. You will sometimes hear it called "industrial chrome plating," "functional chrome plating" or "engineering chrome plating." Let's look at some of the ways it differs from decorative, or "bright" chrome plating, used on objects like refrigerator door handles and automobile trim to give them a deep, reflective shine.
First, a bit of terminology. The plating industry has historically referred to plating thickness in units called "mils". One mil means simply one thousandth of an inch (0.001 inch).* (*In many parts of the world, plating thickness is expressed in microns (μ). One mil is equivalent to 25.4 microns.)
A typical hard chrome deposit on a newly manufactured part is usually around 3 mils (0.003 inch), or a bit less. This is equivalent to the thickness of an average coat of paint. When repairing a worn part, a much thicker coating – as much as twenty to fifty mils — is sometimes applied. The part is then ground down to the required dimensions.
In contrast, decorative chrome is applied in a much, much thinner layer than hard chrome, typically less than 50 millionths of an inch (0.00003 inch). That's only one hundredth of the thickness of a 3 mil deposit of hard chrome! Decorative chrome is used on many commercial products, including automobiles, to provide an aesthetically pleasing look to metal or plastic parts.
There are other differences between the two types of coatings besides thickness. One such difference involves the chemical form of the chrome dissolved in the plating bath. Hard chrome is always deposited from a strongly acidic bath in which the chrome is in the highly oxidized plus six, or "hexavalent" state. Decorative chrome can be applied either from a hexavalent bath, or from a less toxic bath using chrome in the plus three, or "trivalent" oxidation state. There is research underway into methods that will allow hard chrome to be plated from trivalent baths, but these methods are not yet in widespread use.
Another difference between hard chrome and decorative chrome is whether they are deposited directly on the part or on intermediate layers. Hard chrome is generally deposited directly on the workpiece. Decorative chrome is typically deposited over other plated layers. In earlier years, it was common to deposit a layer of copper, and then a layer of nickel, before depositing the bright chrome layer. Now, it is more common to use only a nickel layer between the bright chrome and the substrate.
The surfaces of products that are manufactured for industrial, commercial or consumer use must often meet certain requirements in order to function properly, or last longer in service use. For instance, if you leave a backhoe with an unplated steel hydraulic rod outdoors, exposed to rain or coastal salt air, it would corrode pretty quickly. However, the same rod plated with two mils of hard chromium will have much better corrosion resistance. Additionally other properties of the deposit, like high hardness, low coefficient of friction, and good oil retention, will prolong the life expectancy of the rod significantly.
You might be asking: "Why not just manufacture the entire part using materials that exhibit the desired properties, and skip the plating process altogether?"
Some parts are made this way. If the hydraulic piston rod in the previous example were made from 300-series stainless steel, for instance, it would hold up pretty well to the elements. But, the cost of manufacturing the part from an expensive alloy would be much higher. And even though the corrosion resistance might be good, the hardness at the outer skin of the rod would likely be less than the hardness of the chromium deposit, making it more susceptible to surface damage. The higher lubricity and lower coefficient of friction exhibited by the chrome coating would tend to make the cylinder's seals last longer, without leaking hydraulic fluid.
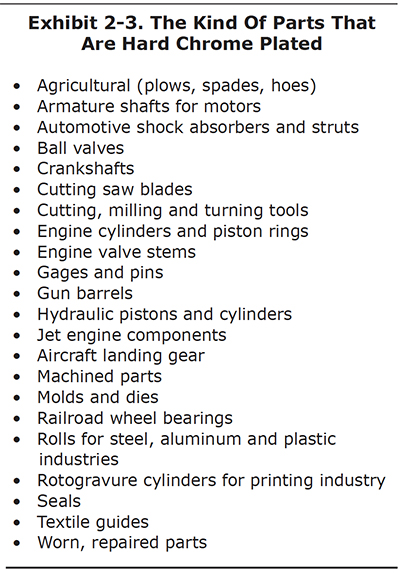
It would be difficult to live a single day in the modern world without encountering parts that have been hard chrome plated, or that were manufactured using plated components. Here are some examples:
The plastic casing for the alarm clock that woke you up was injected from a chrome plated mold. So were parts from your electric shaver, the telephone, the television, the laptop computer and many other household parts. Did you get the morning newspaper? It was printed by a chrome plated rotogravure roll.
When you started your automobile, were you aware that your engine's piston rings and shock struts were hard chrome plated? Perhaps your door handles are decorative chrome plated. Surely most of the rubber Orings and caliper boots were transfer-molded using chrome plated molds and dies. When you drove through the construction zone, did you see the chrome plating on the hydraulic cylinders for the backhoe and bulldozer? Many of the turbine engine components on that jet overhead are plated with chrome, as well as the molds used in making the turbine's blades.
As you wait at the train crossing, it's a safe bet to assume that many of the tapered roller bearings for the train wheels were plated with a thin layer of hard chrome on the inside bore as part of their repair and maintenance process.
Even the fibers that make up the material for your clothing were manufactured using hard chrome plated components.
A list of common parts that are hard chrome plated is shown in Exhibit 2-3.
The file test at the beginning of this section served as a simple demonstration of the benefi cial hardness, abrasion resistance and low coeffi cient of friction for hard chromium. But it has other desirable properties also.
- If two metallic objects rub against one another in service, it's a good idea to plate the most critical or expensive one with chrome. It will have a long life, with minimal wear, and nearly all the wear will occur on the unplated part.
- The melting point of chromium is around 1,900°C, or 3,452°F. This makes it ideal for high temperature applications, such as jet engine turbine components. Chromium conducts heat very well, making it a good choice in hot environments, where heat needs to be conveyed away from a source. The rate of thermal expansion and contraction for chromium is close to many common materials, allowing them to be coated with a metal that reacts similarly during heating and cooling cycles.
- The corrosion resistance of chromium is not as good as metals like gold, silver, copper and nickel. But if the chrome coating is thick enough, it does a pretty good job of protecting metals like steel when exposed to moist air.
- Chrome plating is also used to coat surfaces designed to shield electronics from radio frequency interference and electromagnetic interference.
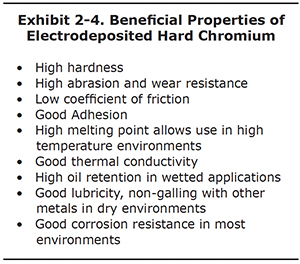
Let's discuss some of chromium's properties in more detail (see Exhibit 2-4). First we'll talk about how to measure the properties of chromium deposits, starting with hardness.
As the name implies, hard chrome is notable for its hardness. In fact, chrome is so hard that measuring its hardness presents some challenges.
You can think of hardness as being the resistance of a material to deformation when you try to compress a small area on its surface. There are several ways to measure that resistance. In one common method, called Rockwell hardness, you press a steel ball or other indenter into the surface and see how deep it goes. Rockwell hardness testers are in common use for measuring the hardness of metals such as steel. But they are not suitable for chromium.
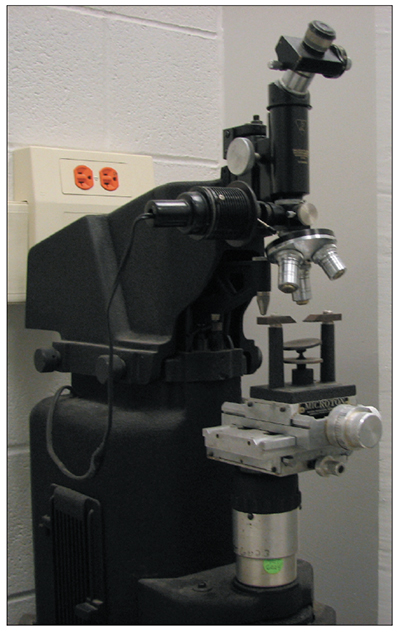
Exhibit 2-5. Vickers micro hardness tester.
Instead, you generally measure chrome hardness by forcing a much sharper, pin type indenter into the surface, and using a microscope to measure the size of the impression it leaves. These are referred to as micro hardness testers. The results are typically expressed in Brinell, Vickers or Knoop units depending on the type of equipment used for the measurement. A Vickers hardness tester is shown in Exhibit 2-5. The hardness of various materials is shown in Exhibit 2-6. An example of a Vickers hardness impression is shown in Exhibit 2-7.
The actual hardness of any plated deposit depends on many factors, including plating conditions. For example, typical bright chromium deposits can range anywhere between 950 and 1,200 on the Vickers scale. Generally, bright chromium deposits are harder than dull deposits, which typically have a hardness around 600 VHN. Later in the course, we will cover the best conditions for making bright, hard chrome deposits.
Additional information on hardness is available in ASTM B578 (microhardness of electroplated coatings ) and ASTM E384 (microindentation hardness of materials).
Hardness thus provides a handy way to check that your plating process is performing as expected. But hardness in and of itself is not usually the most important functional characteristic of the surface. More often, what you're really after is abrasion resistance. Let's consider that next.
![]() |
![]() |
Abrasion Resistance
Parts are often chrome plated so that they don't wear out so fast. A few thousandths of an inch of chromium can increase the useful life of a part four to five fold (see Exhibit 2-8 & 2-9). This is especially true for parts that have any kind of moving contact with other surfaces.
Examples include:
- valves and piston rings in engines
- mold cavities for the plastic and rubber industries
- rollers for printing, and for the plastic, steel and aluminum industries
- chainsaw cutting edges
![]() |
||
Exhibit 2-8. Upnlated hydraulic piston that has severe wear after only 50 hours of service. | Exhibit 2-9. Chrome plated hydraulic piston that shows no signs of wear after 500 hours of service. | Exhibit 2-10. Taber wear tester measures abrasion wear resistance in a non-lubricated environment. For additional information, see ASTM D4060. |
Abrasion resistance is typically measured by rubbing surfaces together and seeing how much material is lost. Such testing is time consuming and expensive, which is why hardness is often used as a more economical way to estimate abrasion resistance. But it is not always true that the harder the surface, the better. In fact, slightly softer chrome deposits, in the 750 to 800 Vickers range, have been found to wear better than harder, more highly stressed deposits. One theory holds that the very hardest surfaces tend to fracture into tiny, highly abrasive micro crystals. But this is still a research question. The fact remains that chrome coatings in general are among the most abrasion-resistant surfaces in common use today.
The Taber wear test (Exhibit 2-10) can be used to express abrasion resistance in a non-lubricated, dry friction environment. In this scenario, hard chrome, deposited under conditions that maximize dry wear, will lose only 2 or 3 milligrams of coating material for every 1000 cycles of testing, which translates to a Taber wear index value of 2–3. The lower the wear index, the better the abrasion resistance.
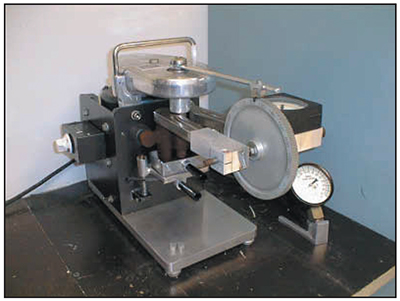
Exhibit 2-11. Falex wear tester simulates and measures wear in a lubricated environment.
Similarly, the Falex wear test (Exhibit 2-11) can be used to measure wear in a lubricated environment. In the test, a chrome plated pin rotates at 290 rpm in pressurized contact with a pair of steel blocks.
Low Coefficient of Friction
Hard chrome can be used to reduce friction in applications where unlubricated metal parts rub against one another in use. For example, a machine with chrome plated guides, slides or rollers will require less energy to start or maintain motion.
Good Adhesion
An important property of hard chromium plating is its good adhesion or bonding to the base metal. Without this property hard chrome could not be used in applications where coating delamination might have disastrous results, such as aircraft brake rotors. The adequacy of chromium adhesion can be measured by plating a thin sample metal strip or rod and subsequently bending the sample up to 90 degrees. This is referred to as the bend test. The sample passes the test if the chromium layer at the bend remains adhered to the base metal. Another adhesion test involves grinding a portion of a plated sample down to the base metal and examining the base metal /plating interface under magnification to assure that the chromium remains bonded to the base metal.
Adhesion problems associated with hard chrome plating have been observed and are discussed later in this course. These problems typically arise from either inadequate cleaning or improper activation/reverse etch.
For additional information on adhesion, see ASTM B571 (Adhesion testing of metallic coatings) and the federal hard chromium specification QQ-C-320 Admendment 4.
High Oil Retention
In lubricated environments, hard chrome has an additional advantage, not shared by most other coatings. When hard chrome is plated onto a surface, the plated layer tends to be shot through with a web of tiny cracks, called "microcracks." This network of cracks relieves internal stress in what would otherwise be a brittle coating. But when a lubricant is present, the microcracks serve an additional purpose – they help retain lubricant on the surface of the plated layer. Chromium plated parts are sometimes run anodically (reverse) for a short period (about 60 seconds) during the plating cycle to open up microcracks and provide channels for oil retention. In the case of hydraulic cylinder rods, for example, the microcracks in hard chrome plated rods hold hydraulic fluid after the seals wipe the rod during extension (see Exhibit 2-12). This makes the seals last longer, since the oil is still present on the surface of the rod to lubricate the seals when the rod is retracted. Retained lubricant also enhances corrosion resistance of the base material.
Exhibit 2-13 is a photograph that depicts microcracking. Exhibit 2-14 is a microsection (cross-section) of the same specimen.
![]() |
||
Exhibit 2-12. The hydraulic seals inside of the packing gland (middle in photo) last longer because the microcracks in the hard chrome plated rod trap hydraulic oil during service use. | Exhibit 2-13. Surface photograph of chromium plated surface showing microcracking. Courtesy of Hamilton Sundstrand. | Exhibit 2-14. Microsection of chromium deposit with microcracking. Courtesy of Hamilton Sundstrand. |
High Melting Point
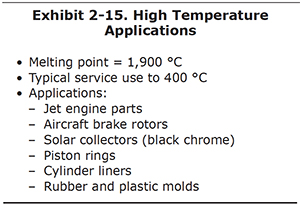
Yet another advantage of hard chrome is its superior temperature performance. Due to its high melting point, chrome plating holds up well in high temperature applications (see Exhibit 2-15). Of course, in typical applications, plated chromium will not ordinarily see temperatures approaching its melting point. But it can generally stand up to higher temperatures than the materials it is plated on.
For example, many components in jet engines for aircraft are chrome plated. So are many aircraft disc brake rotors, where the frictional forces needed for stopping the craft will build up a lot of heat in the rotors.
Solar collectors are frequently plated with black chromium, and the coating is well suited to the solar heat.
Many molds for the rubber and plastic industry are chrome plated. The chromium plate withstands the high temperatures of the molten material injected into the mold under pressure.
The piston rings or cylinder liners are plated in many internal combustion engine applications. However, note that pistons rings and cylinder liners are never BOTH plated, since hard chrome rubbing on hard chrome will produce a kind of surface damage called "galling."
An important consideration of high temperature environments is that the hardness of chrome deposits decreases as the temperature rises above 600°F.
Thermal Conductivity
Heat sinks are often used to conduct heat away from components that become hot during service use. Copper and aluminum materials are frequently used for this purpose. The silicon controlled rectifiers or SCRs in thyristorbased DC power supplies for electroplating are mounted on aluminum heat sinks. Processor chips for computer motherboards or video adapters typically have copper or aluminum heat sinks mounted on top. Since they are exposed only to air, they don't corrode in their unplated condition.
Similarly, copper and aluminum components are often used in fluid-to-fluid or fluid-to-air heat exchangers. In the case of a fluid-tofluid heat exchanger, a pipe or coil carrying one fluid is installed inside a vessel filled with another liquid. In the case of a fluid-to-air heat exchanger, a fluid is pumped through a piping system that has air or another gaseous medium blowing across.
Sometimes heat sinks or heat exchangers are needed in an environment where a fluid or gas will chemically attack the base metal. So long as the chromium is resistant to chemical attack in its environment, it makes good sense to chrome plate the heat sinks or exchangers. The chromium serves as a barrier to corrosion and also conducts heat well, making the heat transfer process more efficient.
Lubricity
In plastic and rubber molding, molten material is injected under high pressure into heated metallic molds (Exhibits 2-16 and 2-17). After the molds are cooled, they are separated to permit the removal of the molded parts. Chrome plated molds are common, because the chromium deposit has good release properties. This makes it easier to eject the parts from the mold, and reduces damage to the parts. Chrome plated molds generally last many more cycles than unplated ones. Molds are usually replated many times to extend the life of the expensive mold.
![]() |
![]() |
Exhibit 2-16. Plastic injection molds are often chrome plated so the product will easily release from the mold. | Exhibit 2-17. Some small rubber molds that are flash plated with chromium. |
Corrosion Resistance
In addition to wear resistance and good high temperature performance, chrome coatings can provide some corrosion protection. The recommended minimum thickness of hard chrome, when used for protection against corrosion is 2 mils (0.002 in).* (*AMS 2406, paragraph 8.7.) Electrodeposited chromium quickly forms a thin oxide film when exposed to air or oxidizing agents. This oxide film acts as a barrier to many corrosive materials that it may come in contact with. It is even more helpful that the oxide film reforms after the chrome is scratched or scraped. This makes it well-suited for use in abrasive environments.
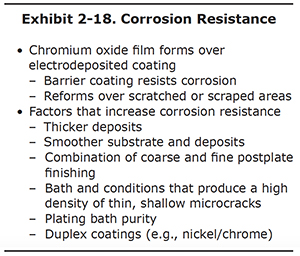
Hard chrome deposits are not all equal with respect to corrosion or chemical resistance. In general, thicker chrome deposits afford more corrosion protection than thinner ones. Also, it's best to have a smooth substrate surface before plating and a smooth deposit after plating. Postplate grinding or polishing will often expose pits that lie underneath nodules, and the pits are points of corrosion. These factors are summarized in Exhibit 2-18.
One other subject should be covered when talking about postplate grinding or polishing. Both coarse and fine finishing techniques are needed. The coarse phase smears the metallic chromium to cover over voids and cracks. The shallow cracks, generally called "microcracks," are the ones that we mentioned previously in discussing their ability to retain lubricants. These microcracks are invisible to the naked eye. In contrast to microcracks, large cracks, often referred to as macro-cracks, are highly undesirable and typically result in very poor corrosion resistance. Large cracks can often extend all the way from the surface of the coating right through to the substrate material, exposing the substrate directly to air or water, causing corrosion and providing a place where the coating can begin to peel away from the surface.
Iron, copper, aluminum and other metallic impurities in the plating bath tend to decrease the corrosion resistance of the deposit. Bath replacement or purification may be needed when an older bath fails to deposit chromium that is suitable for service use.
Final grinding of the chrome plating can increase the number of cracks in the deposit. For greater corrosion resistance, based upon equal thickness unground deposits should be selected if possible.* (*QQ-C-320 paragraph 6.1.2.)
Increased corrosion resistance can also be attained by using a duplex coating, such as a nickel deposit followed by a chrome deposit. Hard chrome plating is chemically resistant to many common liquids and gases in our environment.
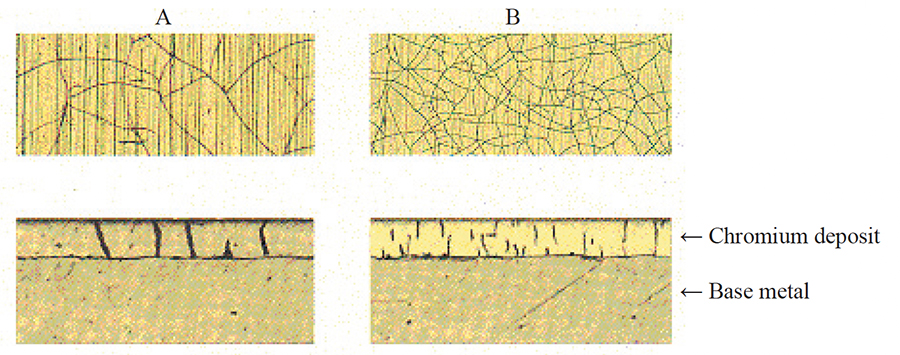
Exhibit 2-19. The pictures show the structure of two chromium deposits (A and B) at the surface (top) and in cross-section (bottom). Deposit A has a macro-cracked layer. It has a small number of deep, wide cracks that penetrate the full layer thickness, causing quick corrosion of the base material. Deposit B has a microcracked structure and has much improved corrosion resistance.
Corrosion resistance for chromium is good for:
- Freshwater
- Air, oxygen
- Steam, moisture
- Milk
- Beer
- Alkaline cleaning solutions
- Gasoline
- Printing inks
- Most organic acids
- Most gases (oxygen, sulfur)
Corrosion resistance for chromium is NOT good for:
- Hydrochloric (muriatic) acid
- Hydrofluoric acid
- Liquids with chloride salts
- Sulfuric acid (especially if heated)
- Phosphoric acid
- Nitric acid (attacked slowly)
Although chrome coatings provide good corrosion resistance in many environments, there are also several common materials, typically acids, that will attack hard chrome deposits. For example, hydrochloric acid, which is also called muriatic acid, attacks chrome very quickly. In fact, muriatic acid is intentionally used to strip chromium.
That concludes our general overview of hard chrome coatings. Now we will go into a more detailed discussion of how to get the best results in hard chrome plating processes, and how to carry out the processes with minimum impact on operating equipment, personnel, and the environment.