Hard Chrome Plating Training Course
Section 6—Plating Bath Fitness
Hard chrome plating baths are durable, especially those with standard chromic acid/sulfate chemistry. Most facilities are able to maintain these baths near peak performance for 10 years or longer by preventing contamination, making the appropriate chemical additions, and occasionally treating for impurities. On the other hand, mistreated and neglected hard chrome baths plate slowly, are a source of plating rejects and are costly in terms of energy use and eventually disposal costs.
The purpose of this section is to tell you what you need to know to keep your hard chrome baths in
good shape and, most importantly, to prevent unnecessary contamination. Of course, no matter how meticulous you are
at prevention, some level of contamination will inevitably occur. This section also covers methods and technologies
to remove the most common contaminants.
Analytical Data
Before beginning the discussion of bath contamination, we are going to talk about data. When you visit the doctor for a physical he takes blood samples and sends those to the lab for analytical tests. Using test results, the doctor can accurately evaluate your health. Like a human body, the condition of your hard chrome bath can also be tracked by analytical tests performed at regular intervals. In this section we are going to discuss what plating bath tests are needed, and how to use test results.
The Basics
In Section 3 we learned about the chemistry of hard chrome baths, in particular the standard chromic acid/sulfate bath. To make up this bath, chromium trioxide and a small amount of sulfuric acid are added to water until the concentration is 33 oz/gal of chromic acid and 0.33 ounces per gallon of sulfate, a 100 to 1 ratio.
We also learned that the chrome in a fresh bath is in the hexavalent form (Cr+6), which gives a new bath its bright orange color.
Once the bath is put into service, some of the hexavalent chromium (Cr+6) is converted to trivalent chromium (Cr+3), which has a green color and when combined with the bright orange it turns the bath a brownish orange. Some trivalent chromium is okay, but if too much chrome is in that form, the plating rate goes down and other problems will occur. As a rule of thumb, the Cr+3 concentration should be no higher than 1 oz/gal.
The most basic analytical tests performed for hard chrome baths include:
- Chromic acid (CrO3)
- Trivalent chromium (Cr+3)
- Sulfate (SO4)
Using these data, you can determine if:
- the amount of chrome in the bath is correct (chromic acid should be around 33 oz/gal)
- the amount of sulfate in the bath is correct (total SO4 should be around 0.33 oz/gal)
- the chromic acid to sulfate ratio is correct (close to 100:1)
- trivalent chrome is in check (should be less than 1 oz/gal Cr+3)
Impurities
![]() |
![]() |
![]() |
![]() |
In addition to the basic parameters, there are other chemical tests that should be performed to determine the health status of your bath. We will refer to these as impurities, since they are chemicals that you didn't intentionally add to the bath. The most common impurities include:
- tramp metals (mainly iron, copper, and aluminum)
- chloride
- suspended solids
- oil and grease
Here are some of the common ways that impurities can find their way into the bath:
- Tramp metals are introduced to the bath primarily as a result of reverse etching and corrosion of bus bars and racks.
- Chloride is introduced from various sources, with the most common being city water used for evaporative makeup, and drag-in from processes such as acid cleaning and nickel plating.
- Suspended solids are tiny particles in the bath that don't dissolve. These are contributed from various sources such as airborne dust, flaking of anodes, and poor housekeeping practices.
- Oil and grease can be added to the bath by inadequately cleaned parts.
Reading Lab Reports and Using the Data
Units of Measure. As an electroplater, you are going to come across different units of measure for bath chemicals and impurities (Exhibit 6-1). Each of these can be converted to the units you are comfortable working with. During this course, we use both English units (such as ounces per gallon) and metric units (such as grams per liter and milligrams per liter). Laboratory reports are usually in metric units. (Sometimes values are expressed as percentages, which would be the same in any units). In any case, it is important for you to be able to convert from one unit of measure to another. That way, you can make better use of information from various sources such as labs, journal articles, books, suppliers and consultants. In the following discussion, we will show you how to convert these units.
Let's learn from an example. A common rule of thumb for platers is to keep the trivalent chromium concentration in a hard chrome bath below 1 oz/gal. The equivalent of 1 oz/gal for other units of measure is shown in Exhibit 6-2. Also shown in parentheses is the multiplier used to arrive at the equivalent value.
Let's try a new example,
- To convert 0.5 oz/gal to grams per liter, multiple 0.5 times 7.5, and you arrive at 3.75 g/L.
- To convert 0.5 oz/gal to percent, multiple 0.5 times 0.75, and you arrive at 0.375 percent.
- To convert 0.5 oz/gal to milligrams per liter, multiple 0.5 times 7,500, and you arrive at 3,750 mg/L.
- To convert 0.5 oz/gal to parts per million, multiple 0.5 times 7,500, and you arrive at 3,750 ppm.
Now, let's start with grams per liter and convert to the other common units.
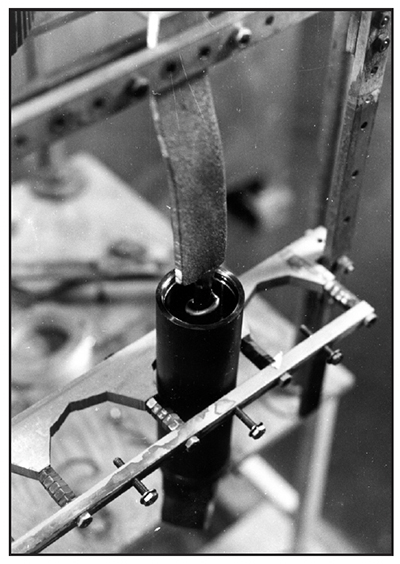
Exhibit 6-5. ID PLATING: Trivalent chromium increases because anode has less
area than plated surface
- Formed during plating process at the cathode
- Converted to Cr+6 at the anode
- ID plating causes Cr+3 to increase
- Ways to reduce Cr+3:
- Plate more ODs than IDs
- Use "waffle" anode material with high surface area
- Dummy the bath or use porous pot
Let's use 10 g/L as an example.
- To convert 10 g/L to ounces per gallon, divide 10 by 7.5 and arrive at 1.3 oz/gal.
- To convert 10 g/L to percent, divide by 10 and arrive at 1%. An easy way to make this conversion is to simply move the decimal point one place to the left.
- To convert 10 g/L to mg/L, multiply by 1,000 and arrive at 10,000 mg/L. An easy way to make this conversion is to simply move the decimal point three places to the right.
- Since milligrams per liter and parts per million are the equal, use the same procedure to convert 10 g/L to ppm; multiply by 1,000 or simply move the decimal point three places to the right.
A summary chart showing various unit conversions can be found in Appendix 10.
Chemical Abbreviations. When you received a laboratory report, it may spell out the chemicals or just use abbreviations. Exhibit 6-3 shows abbreviations for the common chemicals and impurities found in chrome plating baths.
Using Lab Data. The health of your plating bath can be tracked by analyzing samples of your bath at regular intervals. How often should you have the bath analyzed? The answer depends mainly on your workload. For most shops, chromium (total and trivalent) and sulfate should be checked at least once a month and impurities should be checked every three months. Shops with high workloads should check chromium and sulfate weekly. Longer intervals between analyses for impurities are ok (e.g., annually) if you can establish that their build-up rate is slow.
Save all of your lab reports and put them to use by generating graphs that track the concentration of impurities over time. Using the graphs, you can identify potential problem areas before they get out of hand.
The sample graph in Exhibit 6-4 shows iron concentration over a two year period. Check with your lab; they may be
able to generate graphs like this automatically using their software.
In the next discussion we will cover the causes and problems associated with trivalent chromium, tramp metals,
chloride and other impurities in the chrome plating bath. Then we will look at ways of preventing bath contamination
and ways of treating contaminated baths.
Trivalent Chromium (Cr+3)
Hexavalent chromium (Cr+6) is the form of chromium that is needed for plating parts. Having some trivalent chromium is okay, but too much can cause plating problems and increase your use of energy.
Trivalent chromium is formed during the plating process. When chromium is deposited onto the part, a small amount of
trivalent chromium
is formed near the cathode. Simultaneously, a nearly equal amount of trivalent chromium is converted to hexavalent
chromium at the anode. Therefore, since trivalent chromium is being both created and converted back to hexavalent
chromium, in most cases, trivalent chromium stays at an acceptable level.
However, in cases where your anode surface area is smaller than your cathode surface area, you may be generating trivalent chromium faster than you are converting it back to hexavalent chromium. When this happens, the trivalent chromium concentration is going to rise.
An increase in trivalent chromium is most commonly caused by plating inside diameters (IDs). If you think about it,
that makes sense. When you plate an inside diameter, you insert the anode into the part. The outside diameter (OD)
of the anode has to be smaller than the ID of the part if the anode is going to fit inside it (Exhibit 6-5).
Therefore, you will generate more trivalent chromium on the surface of
the part than you are converting back to hexavalent chromium on the anode.
To alleviate this problem, you can alternate use of a tank by plating both IDs and ODs. For example, use the tank for
IDs one day and ODs the next day.
Another way to keep down the Cr+3 level is to use waffle shaped lead mats instead of lead bars for anodes.
The waffle type of material has a greater surface area than stick anodes and therefore, it converts more
Cr+3 back to Cr+6 than the stick anodes.
If Cr+3 gets out of control then you may need to dummy the bath or use a porous pot to lower the Cr+3 level. These methods are discussed later in this section.
![]() |
![]() |
Metallic Impurities – Tramp Metals
Iron, copper, aluminum and other metallic impurities are often referred to by chrome platers as "tramp metals." Unlike trivalent chromium, the tramp metals have no business being in the chrome bath. They enter the bath in various ways and if their concentration gets sufficiently high, they will cause plating problems and increase your use of energy.
The most common tramp metal is iron, and it is mainly contributed by reverse etching. Copper is usually the second most prominent tramp metal and it is contributed mainly by corrosion of bus bars, hooks and other exposed copper surfaces (e.g., scrubbing the copper bus bar and allowing the residue to enter the bath). Aluminum can also be seen at significant levels, especially in shops that use aluminum racks. Zinc is usually not seen at high levels except at shops that use the zincate process for chrome plating aluminum parts.
Prevention is much less expensive than treatment and it should therefore be your first line of defense. Installing a dedicated reverse etch tank can add many years of life to your plating solution. With this approach, all reverse etching is done in one tank. The parts are then plated in other tanks. The reverse etch solution can be operated at a very high level of metallic impurities without significant impact. You might find that you can operate for years before the solution needs to be discarded.
Here are some additional hints:
- Nickel plate copper and aluminum bars that come into contact with chromic acid.
- If parts or racks fall to the bottom of the chrome tank, retrieve them immediately.
Treatment methods for tramp metals include the porous pot, membrane technologies and ion exchange. These methods are discussed later in this section.
Metallic Impurity Limits
Hard chrome baths will continue to plate at a metallic impurity level over 20 g/L. However, when impurities reach that level, the efficiency of the process is extremely low, which translates to high energy costs. Also, if you plate with a bath that contains significant contamination levels, you are almost certain to start seeing plating problems. So, what should you set as your maximum limit?
You will hear many different opinions on this subject. The values shown in Exhibit 6-6 are ones that we feel are acceptable. They are 7.5 g/L for trivalent chromium and 7.5 g/L for tramp metals.
Although each of the metallic impurities has its own special way of causing plating problems, they also have a combined effect – each impurity can make the bath more sensitive to the presence of other impurities. Therefore, we do not recommend allowing both trivalent chromium and tramp metals to reach the 7.5 g/L limit at the same time. You should also set a limit on the combined number that results if you add together the concentrations of Cr+3 and the tramp metals. We suggest an upper limit of 10.0 g/L for the combined number.
Keep in mind, that these are upper limits. They are not recommended as good operating levels. To be certain that impurities are not affecting your plating, we suggest that you cut these numbers in half and try to stay below them.
Next, we will discuss treatment methods for removing trivalent chromium and tramp metals. The most common methods include:
- Dummy plating
- Ion transfer (includes porous pot)
- Membrane technologies and
- Ion exchange.
Dummy Plating
Dummy plating is used to convert trivalent chromium to hexavalent chromium. It also will remove chloride from the bath by converting it to chlorine gas. Remember that trivalent chromium is generated when the anode surface area is less than the cathode surface area, as with inside diameter (ID) plating. Dummy plating is just the opposite. The lead anode surface is made very large in comparison to the cathode area. Typically a 10:1 to 30:1 anode to cathode surface area is used. This can be achieved by loading the tank with stick anodes or more easily using sheets of the waffle type anode material and using a dummy part such as a small sheet of copper as the cathode. During plating, a current density of 8 to 15 amps per square inch is applied.
Dummy plating or "dummying the bath" is usually performed during off hours so not to interfere with production. A good target level of trivalent chromium to shoot for is 3.8 g/L or less. It is recommended that you take bath samples before and after the process to determine its effectiveness. The analytical results will help you determine how long to perform the process the next time it is needed. You want to pick a time duration that is long enough to convert the required amount of trivalent chromium back to the hexavalent state, but you don't want to waste energy or needlessly plate out chromium.
Ion Transfer-Porous Pot
The most popular device on the market for chrome bath purification is the porous pot. These units cost $700 to $1,200, depending on size. They are placed into the chrome plating tank and are powered by the tank rectifier. The unit shown in Exhibit 6-7 is designed for a 2-bus bar tank, but other configurations are possible. The unit includes:
- unglazed ceramic pot,
- internal lead cathode,
- external lead anode
In theory, trivalent chromium is oxidized at the anode and iron and other dissolved tramp metals migrate from the bath through the ceramic pot, toward the cathode. The metals that migrate into the pot precipitate as a sludge. Periodically, the unit must be removed from the tank and cleaned out. The solution in the pot can be returned to the bath and the sludge must be placed in a hazardous waste drum for off-site disposal.
This unit does a reasonably good job of oxidizing trivalent chromium to hexavalent chromium. However, this can also be accomplished by simply dummy plating your bath during idle hours. The porous pot is not very effective for removing tramp metals unless your tramp metal concentration is very high, say above 10 g/L to 15 g/L or about 1.3 to 2.0 oz/gal. Most shops try not to let their tanks get this contaminated, but if you can operate in this range, then the porous pot could be a useful technology.
However, for shops that want to operate with tramp metals below 7.5 g/L (1 oz/gal), you need to look at an alternative technology.
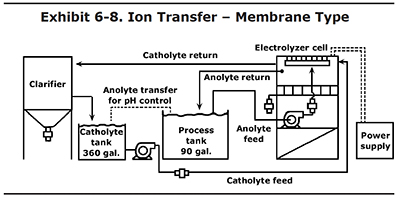
Ion Transfer – Membrane Type
Another type of ion transfer technology is show here. Unlike the porous pot, it uses external tanks (see Exhibit 6-8).
With this system, chromic acid is transferred from the plating tank to an electrolyzer cell. The electrolyzer cell contains anode and cathode compartments, separated by a plastic membrane. The plating solution goes into anode compartments and fresh chromic acid is circulated in the cathode compartments. In theory, dissolved tramp metals are electrically driven through the membrane and captured in the catholyte solution, where they are removed by gravity in a clarifier.
This type of system has results similar to the porous pot. It can remove tramp metals when they are at a high concentration, but is unable to keep a bath in the desired range of less than 1 oz/gal. Also, like the porous pot, it does a reasonably good job of converting trivalent chromium back to hexavalent chromium.
Advanced Membrane Technologies
Membrane technologies work much like the porous pot. However, instead of using a ceramic pot, the anode and cathode are separated by a membrane, which looks like a fabric. Different types of membranes are used for this purpose. The most popular one is Nafion, a material manufactured by DuPont. This membrane allows cations, like tramp metals, to pass through, but prevents anions, like hexavalent chromium from passing.
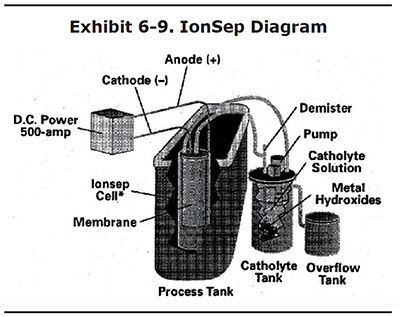
Different chemicals have been used in the cathode compartment. The IonSep Company sold a unit that uses a caustic solution (see Exhibit 6-9). With a caustic catholyte, the tramp metals precipitate as solids when they pass thorough the membrane from the plating bath to the catholyte compartment. This technology is effective for removing tramp metals, even for baths that are operated at 3 g/L of tramp metals or lower. It also converts trivalent chromium to hexavalent chromium at the anode, in a manner similar to the porous pot. Unfortunately, this technology is no longer on the market, although IonSep still services the units they previously sold.
Therefore, at this time, there are no known commercial membrane technologies that are designed for purification of hard chrome plating baths. Perhaps a new manufacturer will come along in the future.
Ion Exchange
Ion exchange is the oldest technology used for hard chrome bath purification; it was first applied around 1950. In
operation, a chrome bath is diluted with water, and is then passed through a column containing a special ion
exchange resin that has an affinity for tramp metals. Dilution is necessary because concentrated chromic acid will
shorten the life of the ion exchange resin. As the chrome bath passes through the ion exchange resin, tramp metals
are captured and held onto the surface of resin. After the capacity of the unit is reached, the resin column is
regenerated using sulfuric acid, which pulls the tramp metals
off the resin. The resin column is then rinsed with fresh water. The regeneration and rinsing steps generate liquid
wastes that contain some chromium and must therefore be treated. The purified chrome solution can be added back to
the bath. Even though it is less concentrated than the bath itself, the natural evaporation of the chrome bath
usually allows for its return.
A commercial ion exchange unit used for chromic acid purifications is shown in Exhibit 6-10.
The advantage of ion exchange over other chrome bath purification technologies is that ion exchange can remove the tramp metals to very low concentrations, even below 1 g/L. The drawback of this technology is the volume of waste generated, which is typically too large for shipping offsite. Therefore, the shop must have a wastewater treatment system and a discharge permit.
Chloride
Chloride is introduced from various sources, the most common being city water. Most city water is treated with chlorine, which contributes the chloride. Many shops add city water to their bath on a daily basis to make up for evaporation. Therefore the chloride concentration can build up quickly. Other sources include drag-in from processes such as hydrochloric acid cleaning or activation and nickel plating.
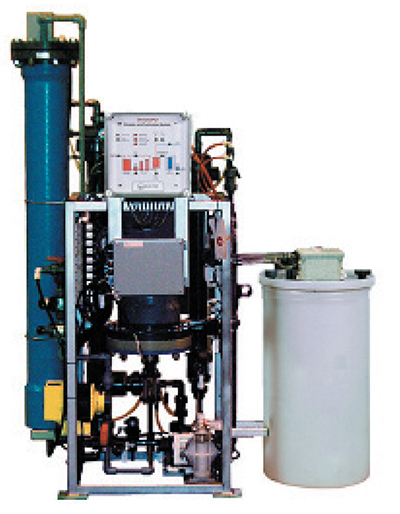
Exhibit 6-10. An ion exchange system designed specifically for purification of chromic acid baths. Courtesy of Eco-Tec.
Small quantities of chloride can cause chrome deposits to have a hazy appearance. The concentration should be kept below 25 mg/L Cl and preferably near 0 mg/L Cl.
To prevent chloride contamination:
- use deionized water for evaporative makeup, and
- improve rinsing after HCl etching or other preplate processing
To remove chloride:
- dummy the bath or use a porous pot, or
- precipitate the chloride using silver oxide
Suspended Solids
Suspended solids are tiny particles in the bath that don't dissolve. These come from various sources, including airborne dust, glass bead/aluminum oxide residuals, flaking of anodes, metal slivers added during reverse etch and poor housekeeping practices. Magnetic particles, or particles that would be attracted to a magnetized part, are particularly damaging since they will likely end up attached to the part. During plating, suspended solids can become imbedded in the chrome deposit and will cause deposit roughness or cause pitting if they are dislodged from the deposit during postplate grinding or polishing.
There are a number of ways in which you can reduce the introduction of suspended solids into your bath:
- improve preplate cleaning practices
- rinse off pumice thoroughly before plating
- relocate blasting cabinets or other equipment that generates dust away from the plating tank
- prevent airborne dust as much as possible, e. g., use a vacuum for cleaning the floor rather than a broom
- cover the tanks when not in use
If a bath is contaminated with suspended solids, they can be removed by:
- filtering the bath continuously using a in-tank filter, or
- filtering the bath periodically by pumping your solution through an external filter
Check with suppliers on the compatibility of their filter media with chromic acid.
Note that some solids in a plating tank are not suspended, but rather sink to the bottom of the tank and form a blanket of sludge. If excessive air or mechanical agitation is used, the sludge will be dispersed in the bath and will increase problems associated with solids. Periodically, you should pump out your chrome solution, remove the bottom 6 to 8 inches of liquid and sludge and return the solution to the tank. The liquid/sludge removed must be disposed of as hazardous waste. When the tank is empty, this is a good opportunity to check the condition of the liner to assure that it is not leaking.
Oil and Grease
Oil and grease is introduced to the bath by inadequately cleaned parts. Some oils will float on the surface of the plating tank. When this occurs, parts entering the tank will pick up a film of oil on the surface. This film may impact chrome coverage or prevent good adhesion of the deposit. Oil and grease contamination also causes a buildup in trivalent chromium. With highly contaminated baths it is very difficult to maintain the Cr+3 concentration below 1 oz/gal (7.5 g/L) even when periodic dummy plating is employed.
The best approach is to prevent oil and grease contamination is to assure that parts are completely clean before entering the plating tank. This means not only the surface being plated, but all wetted surfaces, including inside diameters, holes and recesses.
Depending on the characteristics of the oil and grease, filtering the bath may have some positive effects. However, most filters designed for removing suspended solids will not completely alleviate the problem.