Hard Chrome Plating Training Course
Section 8—Pollution Prevention
Wastes can accumulate pretty quickly in a plating shop. In fact, every part that is plated generates
waste, like rinse water,
used masking materials, and chromium air emissions. Although it is almost impossible to plate without generating
some waste, you can almost always find opportunities to reduce the amount of waste generated.
If you ask two plating shops to plate the same part, you would find that one shop generates more waste than the other one. That's because there are different ways of masking, rinsing, and performing other plating tasks and these various methods have different results in terms of waste generation.
What is Pollution Prevention (P2)?
During this part of the course, we will look at some good plating shop practices that reduce the amount of waste that is generated. These practices are referred to as "pollution prevention" or simply P2, a special term used by EPA and industry. P2 is an environmental strategy that involves reducing waste at the source before it is generated.
P2 can be thought of as the first line of defense against pollution. Once a waste is generated, you must store it, handle it, treat it and/or dispose of it. Each of these tasks takes time and costs money. By implementing P2, you end up with a smaller waste volume and you minimize expenses.
Some examples of P2 methods used in hard chrome shops that we will be discussing include:
- changing the way you rinse parts so that you minimize drag-out and use less water
- using recyclable masking that eliminates masking waste
- adding a reverse etch tank to prevent iron contamination of the plating bath
Pollution prevention does not include treatment or off-site recycling. These are important tools for meeting regulations and protecting the environment, but, they should be reserved for wastes that you can't prevent. Remember, it is much more efficient to avoid generating waste than to deal with it later.
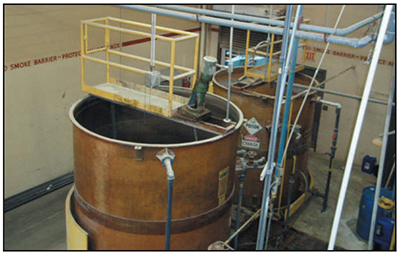
Exhibit 8-1. Wastewater treatment systems remove chromium and other metals from wastewater and generate a hazardous sludge.
Benefits of P2
Pollution prevention makes a lot of sense. It is easy to see that if you generate a smaller amount of waste in the first place, then the entire waste management process is lot easier to deal with. Here are some of the benefits of implementing P2:
- cost reductions, including:
- lower waste treatment costs (Exhibit 8-1)
- less raw material and energy used
- a safer and cleaner workplace
- a better regulatory compliance record, and of course,
- a healthier environment
We will look more closely at some of these benefits.
Saving Money
One of the most obvious benefits of pollution prevention is saving money. Waste is expensive because you have to handle it, store it, treat it, and dispose of it. And the cost can be very significant each step along the way.
One of the most significant potential cost savings measures in any chrome shop is simply preventing chrome solution from entering the wastewater treatment system.
Here's why. If you generate less chrome wastewater, then you use smaller quantities of wastewater treatment
chemicals, which are very expensive. You also reduce the labor required to handle it, and you generate a smaller
volume of hazardous sludge. Sludge is costly to handle, since it must be managed as a hazardous waste, and taken
offsite by a licensed hazardous waste hauler for disposal in an approved facility. Plus, if you keep
the chrome bath in the plating tank in the first place, you don't need to add as much chromium trioxide to the tank.
Here's the most surprising news: for every gallon of chrome solution you keep out of the wastewater treatment system, you save over $100 in chemicals, labor, and sludge disposal.
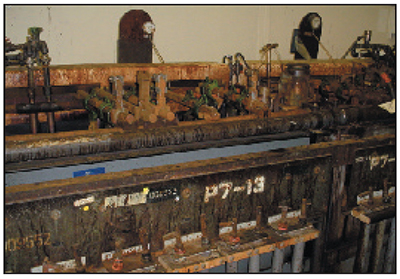
Exhibit 8-2. Hard chrome plating tank covered by drips of chromic acid.
Cleaner, Safer Workplace
Given a choice, everyone would prefer to work in a clean shop rather than a dirty one. A clean shop is a healthier working environment. It is also more efficient, and it produces higher quality plating.
Spills drips and other chrome messes on work surfaces, around the tanks and the floor are basically waste (Exhibit 8-2). Eventually they have to be cleaned up and disposed of. In the meantime, they present a health hazard and create an unpleasant workplace.
The main sources of mess are the process tanks, including plating, stripping and cleaning. The better job you do of preventing pollution at the tanks, the cleaner and safer your shop will be.
Regulations and the Environment
Just about any type of waste you see in a plating shop is covered by state and federal rules. That's because many plating chemicals, like chromic acid, are toxic and therefore can impact human health and the environment.
Environmental regulations apply as soon as a waste is generated and they continue to apply until the waste is safely disposed of. Therefore, the best way to deal with regulations is not to generate a waste at all, or at least to minimize the volume.
Of course, a P2 policy also directly benefits the environment. The less waste we dispose of, the cleaner and safer our communities remain for people, wildlife and plants.
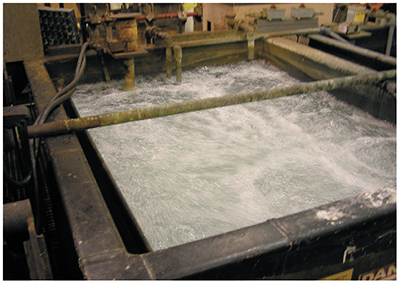
Exhibit 8-3. Well agitated rinse tanks help dislodge drag-out from parts and racks.
P2 in Action
The remainder of this section covers P2 methods that you can implement in your hard chrome shop. These are proven techniques that will pay you back with immediate results.
For the purpose of the course, we have divided the P2 methods into three logical areas:
- Rinse water
- Solid waste
- Air emissions.
Rinse Water P2 Techniques
Rinse water is both a friend and an enemy of the plater.
Rinsing is an important aspect of chrome plating. If the parts and fixtures are not sufficiently rinsed, then when the plater handles the part, chrome solution is going to end up on the plater's hands and clothes. Also, residual solution can cause staining and corrosion of steel parts.
On the other hand, too much rinse water means higher operating costs, and it impacts the environment.
In the following discussion we look at four P2 methods for reducing the amount of rinse water that is used and treated:
- Drag-out reduction
- Counterflow rinsing
- Recovery rinsing
- Good rinsing practices
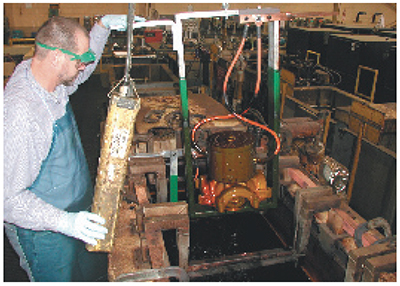
Exhibit 8-4. Skilled plater slowly removing a no-mask anode/part from bath and allowing it to drain off the drag-out.
What is Drag-out?
Drag-out is the plating solution that clings to the parts, racks and fixtures when they are removed from the plating tank.
When an average-sized part is removed from the chrome tank, it can hold as much as a quart of plating solution. Most of that drag-out immediately drips back into the bath. The rest either continues to drip off slowly or stays on the parts and racks as a thin film.
Some parts retain a lot more drag-out than other parts. For example, flat vertical surfaces drain much better than
horizontal or cup-shaped surfaces. Drilled holes also tend
to retain a lot of drag-out, as do masking materials such as tapes or wax.
The objective of rinsing is to remove as much of the drag-out from the part, rack, and fixture as possible. You can meet this objective with less water use if:
- there is less drag-out to remove in the first place, and
- the drag-out can drip freely from the part and rack back into the plating tank.
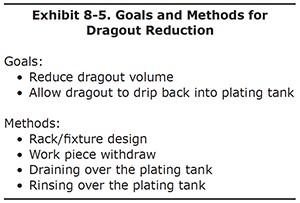
Exhibit 8-5 lists goals and methods for dragout reduction which are addressed in the following discussion.
Rack and Fixture Design
When you are designing a rack or fixture, think about drag-out. You want to avoid creating pockets where drag-out
cannot freely drip back into the tank. Also, avoid horizontal
flat surfaces and holes as much as possible. Another thing to think about is how the part will be oriented on the
rack. You want the part situated in a manner that causes the drag-out to flow freely off the part and back into the
plating tank.
Work Piece Withdraw
When you remove a part from a tank, lift it out of the solution slowly. This trick really works. The thickness of the drag-out layer on the part is thinner if the part is removed slowly from the bath.
Draining Over the Tank
After the part is removed from the plating bath, suspend it over the plating tank until it stops dripping. If you tilt the part to improve drainage, then this will prevent even more drag-out from entering the rinse system.
Rinsing Over the Plating Tank
A small spray of water can also be used at this point to encourage more drag-out to go back into the plating tank. However, if you use recovery rinsing, which will be discussed shortly, you must limit how much water you spray over the tank.
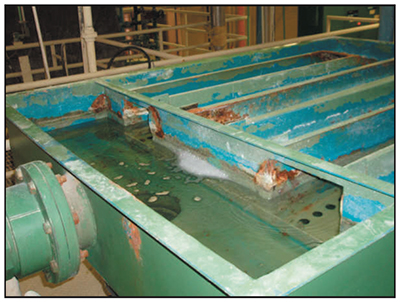
Exhibit 8-6. Only after expensive wastewater treatment can hard chrome rinse waters be discharged from the shop.
Rinsing
We just looked at ways of reducing the volume of drag-out. If we implemented all of those practices, we probably prevented about 75% of the original drag-out from entering the rinse tank. That was a huge savings. But, now, we are going to work on the other 25%.
The drag-out which remained on the part and fixture has started to dry out and create an orange film. The only good way to remove it is to use rinse water.
With rinsing, there are two main objectives:
- We want the part to be as clean as possible, and
- We want to minimize, or if possible completely eliminate, wastewater.
Remember, once the rinse water leaves the rinse tank, it becomes an expensive liability. If we can keep it from going into the drain, then we have prevented pollution and saved money (Exhibit 8-6).
Multiple Rinse Tanks
The use of multiple rinse tanks can reduce water use by 90% or more.
The best use of multiple rinse tanks is the counterflow configuration shown in Exhibit 8-7. With this arrangement, parts are rinsed successively in two or more rinse tanks. The water in first rinse tank becomes concentrated with chromic acid. The last rinse tank must be kept sufficiently clean to do a good job of rinsing.
The more rinse tanks you use, the better this system works. For example, if you have a two rinse tank system, you may need to use 200 gallons of water a day to keep the last rinse tank clean. But, if you add a third tank, you will only need about 20 to 40 gallons of water to do the same job of cleaning the part. Three or four rinse tanks are most common in well designed shops.
When you have a counterflow system like the one in the diagram, it is extremely important that you do not skip rinse tanks. Use each one and use them in the correct order. Otherwise, you will eliminate the benefit of having multiple tanks.
Air agitation of the rinse tanks helps to facilitate or improve rinsing. Also, proper dwell time in each of the rinse tanks is another important factor in improving rinsing efficiency and minimizing fresh water input. Additionally, you can use a conductivity meter in the last rinse tank of the series to control the contamination level of the final rinse and therefore control the volume of water added to the entire rinse system.
![]() |
![]() |
Recovery Rinsing
Recovery rinsing is a counterflow system where the concentrated rinse water in the first tank is used to replenish evaporative losses in the plating tank. Usually, a recovery tank is used in a counterflow tank system like the one shown in Exhibit 8-8.
Recovery rinsing can accomplished with 2 to 4 rinse tanks, depending on how much drag-out you have. If you have a lot of drag-out then you probably need four rinse tanks in order to create a zero discharge system.
A transfer pump is usually used to convey the rinse water from the first rinse to the plating tank, although with small operations it could be accomplished with a bucket. The rinse water in the other rinse tanks gravity flows toward the first rinse.
As with any counterflow rinse system, you must use all the rinse tanks in sequence to get a benefit from multiple tanks.
With this set-up, there is no discharge of rinse water to the treatment system. In fact, many hard chrome shops don't even have a treatment system or a connection to the sewer; they just rely on recovery rinsing. A couple of important notes about recovery rinsing. With a closed loop rinse system such as this, you must deionize the city water before it is used for rinse water. Otherwise, the impurities in the water will build up in the plating tank. Also, it is advisable that you use a dedicated reverse etch tank instead of reversing in the plating tanks. This will prevent a build-up of dissolved iron in your plating solution.
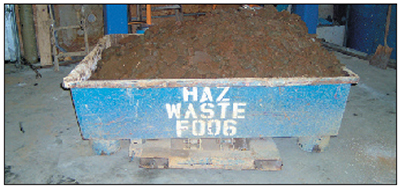
Exhibit 8-9. Hazardous waste sludge generated from treatment of electroplating wastewater.
What is Hazardous Waste?
In 1980, EPA passed regulations that defined hazardous wastes and set out a strict set of rules for how these wastes must be managed and disposed of. Additionally, nearly all states have passed their own set of hazardous waste regulations that are similar to the federal EPA rules.
A waste material is a hazardous waste if it is found on one of EPA's or your state's hazardous waste lists or if it meets certain criteria for being toxic, corrosive, flammable or reactive.
Many wastes generated at chrome plating shops are hazardous. Examples include spent baths, wastewater treatment sludge (Exhibit 8-9), tank bottom sludge, used maskants, and floor sweepings.
Because platers usually have to come into contact with hazardous waste as part of their regular routine, they must receive training for safe handling of this material.
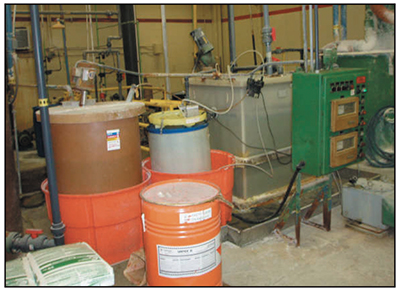
Exhibit 8-10. Wastewater containing hexavalent chromium (Cr+6) must undergo extensive treatment before it can be discharged to the sewer.
Here are some opportunities for reducing hazardous waste from your hard chrome line.
- Drag-out reduction
- Prevent contamination of plating solution
- Waste segregation
- Recyclable masking
- Dry cleanup
- Reduce rejects/rework
Drag-out Reduction
We already talked about how reducing drag-out reduces the generation of wastewater. Well, it can also reduce the
generation of wastewater treatment sludge, which is a hazardous waste. Each gallon of chrome plating solution that
is treated generates up to 100 pounds of hazardous sludge. This material must often be hauled hundreds of miles to
special disposal sites. A single drum of chrome sludge can cost more than $500 to dispose of (Exhibit 8-9).
Therefore, when you implement those drag-out reduction methods we covered earlier, you will not only be cutting down on wastewater generation, you also will be reducing hazardous waste and the associated cost of disposal.
Prevent Bath Contamination
As discussed in Section 6, hard chrome baths are very durable and can last 10 or more years if careful attention is given to preventing contamination and they are properly maintained. If baths are not properly cared for and they are disposed of, it is a very costly event. Disposing of and replacing a 1,000 gallon bath can cost as much as $10,000.
The most common chrome bath contaminant is trivalent chromium (Cr+3). It is formed as
a byproduct of the plating process, when hexavalent chrome is electrochemically reduced at the cathode. In most
situations, trivalent chrome is automatically kept in check because it is reoxidized to hexavalent chromium at the
anode. A buildup of trivalent chrome can occur when a tank is used extensively for inside diameter plating. In this
case, more trivalent chrome is being generated than is being reoxidized. At low concentrations, trivalent chrome
does not present plating problems, however, if it increases beyond recommended levels, it can reduce plating speed
and quality.
Dissolved iron is the second most common contaminant. It is contributed to the bath mainly during reverse etch. Shops that don't retrieve fallen parts and fixtures will also see a buildup in iron from corrosion of these items. Copper is also a problem at some shops, especially where copper bars, used as holding fixtures, are submerged into the plating bath. One way of reducing copper contamination is to nickel-plate any exposed copper, including the tank bus bars. Other metals, such as aluminum and nickel can be found in chrome baths, but usually at low concentrations that do not interfere with plating.
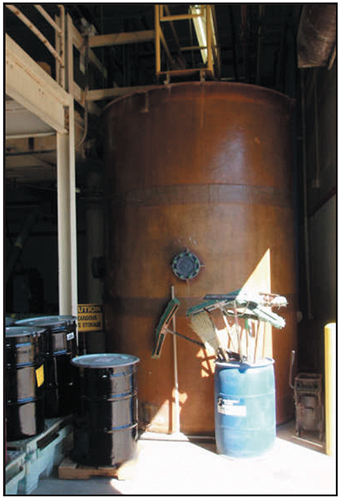
Exhibit 8-11. Using brooms and/or vacuum to clean up rather than water reduces waste volume.
Chloride is another common contaminate. It is added to the bath when city water is used for evaporative makeup.
Bath contamination can impact plating speed and quality. It also adds electrical resistance to the bath, which means that more energy must be used to electroplate the parts.
Here are several commonly used P2 methods that can reduce bath contamination:
- Use dedicated reverse etch tank. This will minimize the amount of iron entering the bath.
- Dummy plating for Cr+3. This can be done on off-shifts or weekends.
- Retrieve fallen parts, racks, clamps and fixtures. These items will slowly corrode and contaminate the bath with tramp metals.
- When cleaning corrosion and dirt from bus bars, for example scrubbing with a ScotchBrite® pad, do not rinse the bars with water or plating solution and allow contaminants to run into the plating bath. This will cause a build up of copper in your bath. Instead, remove the contaminants from the bus bars with a damp cloth.
- Use DI water for evaporative makeup. City water contains chlorides and other chemicals that will buildup in the bath.
Other Methods for Reducing Hazardous Waste
Here are some additional P2 methods that relate to hazardous waste reduction.
Employ Waste Segregation
Waste segregation means not mixing hazardous waste with other solid waste, such as empty containers, newspapers, or office waste. If non-hazardous waste is mixed with hazardous waste, then the entire volume is hazardous, according to EPA regulations. If you are not sure which wastes are hazardous or non-hazardous, ask your supervisor.
Use Dry Cleanup
Dry cleanup methods, including use of absorbents and broom/vacuum, should be used to cleanup spills instead of flushing them with water (Exhibit 8-11). This will minimize the volume of hazardous waste that needs to be discarded. Water should only be used to remove any residual material left behind after using dry cleanup methods.
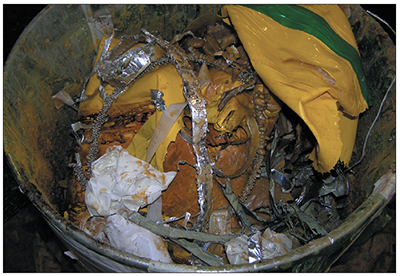
Exhibit 8-12. Used maskant from a hard chrome shop is contaminated with hexavalent chromium and must be disposed of as hazardous waste.
Minimize Maskant Waste
Masking with wax and/or tapes and foils can result in significant volumes of hazardous waste, since these items are contaminated with chrome after use (Exhibit 8-12). Alternative masking methods such as the use of no-mask anodes can eliminate this particular hazardous waste stream.
Reduce Rejects / Rework
Another way of reducing pollution is to cut back on rejects and rework. Mis-plated parts must be stripped and re-plated, which means more drag-out and masking waste. Rework more than doubles the quantity of waste generated for a particular part.
A reasonable goal for hard chrome shops is to reduce rework to less than one out of 20 parts plated (<5%).
An effective way of reducing rejects is to document each occurrence, including recording the tank and rectifier used, plating conditions (e.g., amps/volts, plating time, solution temperature), and noting which fixtures or tooling was used. Over time, these data can be used to identify trends and determine the source of error.
Air Emissions
Chrome plating is notorious for its toxic fumes, which are generated by gassing at the anode and cathode during plating. The gas bubbles, hydrogen and oxygen, rise to the surface of the solution where they burst and release a fine aerosol or mist of hexavalent chromium. This form of chromium can cause cancer if it is frequently inhaled.
To capture chrome aerosols, plating tanks are equipped with exhaust systems that transport the chromium particles to scrubbers, mist eliminators or other types of air pollution control equipment. Many of these units remove the chromium from the air and ultimately transfer it to a wastewater. The wastewater must be treated before it is discharged to a sewer.

Exhibit 8-13. Roof-mounted air scrubber removes chromium from the shop air before it is exhausted to the outside environment.
Air emissions from chrome plating operations are covered by two different federal regulations that work in unison:
- OSHA regulations limit the concentration of hexavalent chromium in the air within the plating shop (these are referred to as fugitive emissions), and
- EPA regulations limit the amount of hexavalent chromium in the air released from the plating shop exhaust stacks (these are referred to as ambient air emissions)(Exhibit 8-13).
In terms of pollution prevention, there are a couple of ways to minimize air emissions and the resultant wastewater generated by air pollution control systems. These include the use of fume suppressants and mist eliminators with recovery systems.
Fume suppressants are chemicals that are added to the chrome bath to reduce the amount of chromium mist generated. There are a number of different types of fume suppressants, including ones that reduce the surface tension of the bath and others that create a chemical blanket on the surface of the bath (Exhibit 8-14).
Mist eliminators are air pollution control devices that cause the chromium aerosols to impinge on a surface where it is removed from the air stream. Periodically, the internal surfaces of mist eliminators must be washed down to remove the film of chromic acid. With some designs, the wash down water is reused in the plating tank, which is a significant P2 measure.
P2 Implementation
Organized P2 Program Participation
To make pollution prevention successful, it generally takes an organized program that is recognized by shop management. It is management's responsibility to make sure that everyone participates. If one or two platers don't follow the procedures, then everyone else's care could be undone. For example, if some platers are rinsing correctly, but others are not draining their racks over the plating tank or are skipping rinse tanks, then the benefits of a counterflow or recovery rinse system are negated.
Written Program / Procedures
It's best to have a written pollution plan with procedures. For example, the plan could state how to perform rinsing,
how to prevent contamination of the plating bath, it could indicate which wastes are segregated and
so forth. The plan could be used to educate all existing workers, and would be a useful training tool when new
people are hired.
The more people that participate in developing the written plan, the better. People who help develop the plan are more likely to see it through.
Measure Progress
It is also a good idea to collect data and measure the success of your program. This may be as simple as measuring the monthly quantity of water used and wastewater treatment sludge generated to measure the effectiveness of your good rinsing procedures. From these values, you can calculate annual savings.
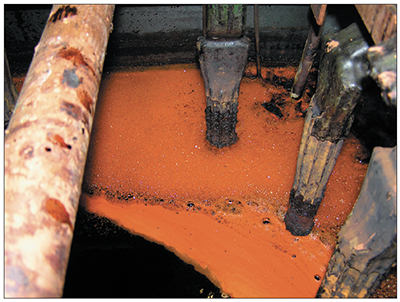
Exhibit 8-14. Fume suppressants added to chrome baths reduce both fugitive and ambient air emissions.
Recognize Success
When concrete results are realized, it is a good idea to communicate these to all the workers, even if it is a marginal improvement. This will help reinforce the importance of following the program and procedures.
P2 Summary
Pollution prevention makes good sense for hard chrome shop owners and workers. Many P2 methods can be implemented at no or low cost. The payback is almost immediate in terms of lower operating costs, a cleaner and safer workplace and community, and a cleaner environment. P2 can impact water, hazardous waste and air pollution. We have discussed some good opportunities for improvement in each of these areas. To help you implement P2, a checklist is presented in Exhibit 8-15. This list contains P2 ideas found in this section as well as other sections of the course.
P2 works best when it is implemented in a formal program and when everyone participates. Whenever possible, measure your improvements and communicate any success to the entire shop.
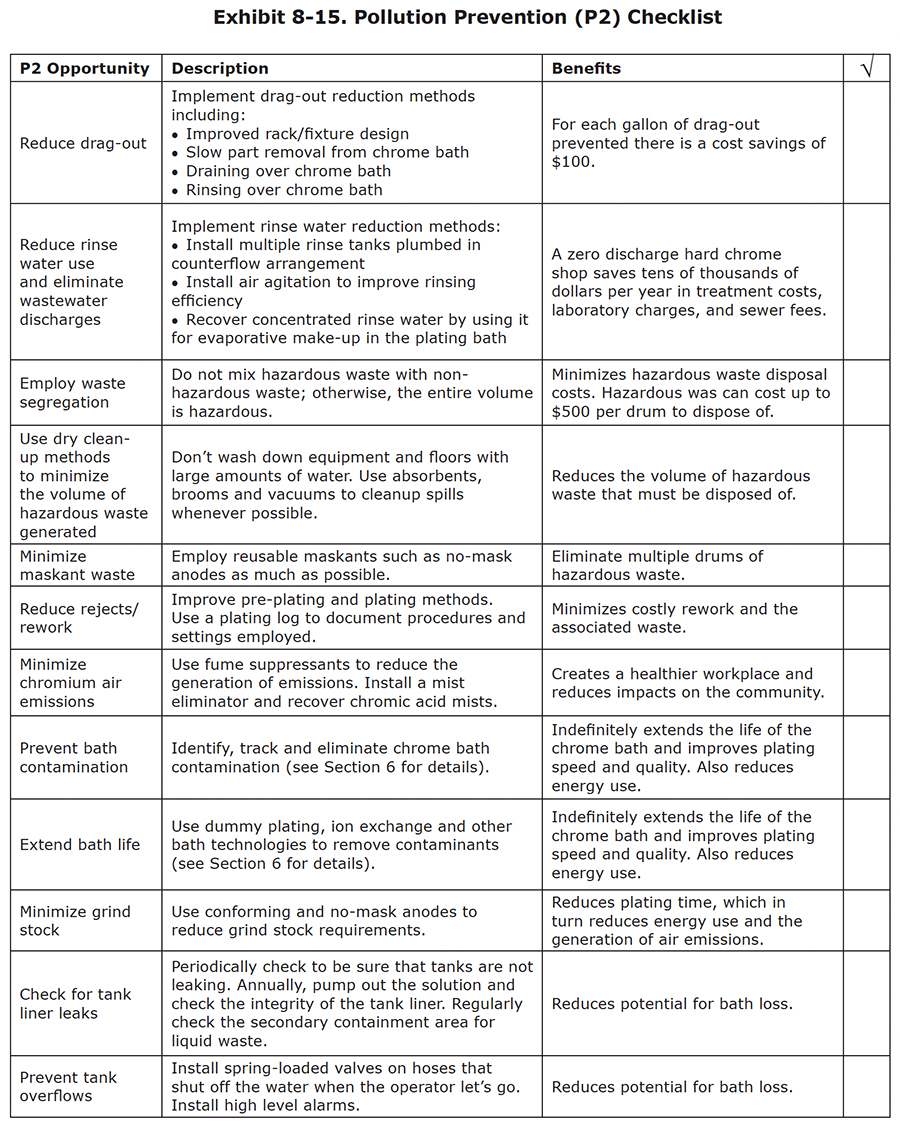