Section 6
Substitute Technologies
6.1 INTRODUCTION
As discussed in Section 3, pollution prevention includes a broad range of approaches and methods. Section 6 focuses on two aspects of pollution prevention: product changes and input material changes. The pollution prevention efforts and experiences of the NCMS/NAMF survey respondents with regard to these two topics have been categorized into six groups:
- Product changes
- Chlorinated solvent use reduction/elimination
- Cyanide use reduction/elimination
- Cadmium use reduction/elimination
- Chromium use reduction/elimination
- Other changes
Product changes made by survey respondents generally involved modifications to parts that resulted in a reduction of dragout (e.g., adding drain holes to parts). A relatively low percentage (8%) of the shops surveyed have utilized this pollution prevention tool. Its limited use is most likely due to the fact that most of the shops surveyed were job shops, which usually have little or no control over the design of the parts they process.
However, the results of the Users Survey did show that respondents have made significant strides in reducing or eliminating the use of chlorinated solvents, cadmium, cyanide and chromium. Sometimes referred to as the four Cs, these materials have been identified by EPA as key targets for control within the metal finishing industry (ref. 415, 416). Although job shops do not have much control over part design, they usually have control over process chemicals. Some exceptions exist, such as instances where aerospace or military specifications require specific finishes, solutions and processing procedures; however, in spite of any limitations, approximately 60 percent of the shops attempted material input changes that potentially reduce or eliminate the use of one or more of the four Cs or another pollutant problem. Based on the comments received from respondents, these changes were made in an effort to reduce the impacts of their processes on the environment and worker health, to help meet environmental regulations and to reduce operating costs.
Although most of the material input changes attempted by survey respondents have been successful, there have been some failures and in many cases, even with successful changes, there have been adverse production impacts. An attempt has been made in this section to summarize the status of change in these areas and to convey the attitudes and concerns of the respondents.
One additional factor to keep in mind when reviewing this section, is that not all of the changes discussed in this section may be improvements. There currently exists a general feeling among regulators, the military and some private industry that all uses of cyanide, cadmium and chromium should be targets for substitution or elimination to meet health and safety and environmental goals. In some cases, the substitutes selected provide a lower quality finish and create new health and safety or environmental problems. In such cases, the question of whether it makes sense to improve the existing process through engineering or through making a substitution must be investigated.
As an example, the hard chromium process has been the target of reduction and/or elimination by the military and private industry (ref. 304, 418, 436). Potential substitutes for this process include: electroless nickel plating (ref. 418, 74), brush plating (ref. 69, 418), nickel alloys and metal spray coatings (ref. 418). In all cases, there is no single substitute that will meet all the requirements of hard chromium plating. Therefore, multiple substitutes must be used, and even then there will remain some applications for which no substitute is available.
Substitutes such as brush plating and nickel alloy plating may reduce the use of chromium, but they usually increase the net quantity of waste generated. These types of solutions are not amenable to recovery or bath maintenance and their by-products must be treated rather than recovered or reused. Conversely, the basic hard chromium bath (chromic acid/sulfate) can be operated in a closed-loop or zero discharge. Chromium can be recovered from rinse water (e.g., recovery rinsing, ion exchange, evaporation), air emissions (mesh pad mist eliminator), and strip solutions (membrane electrolysis) and the baths can be operated indefinitely without discharges (e.g., membrane electrolysis) (Sections 3, 4 and 5 provide information on methods and technologies for closed-loop operation of hard chromium plating). Additionally, parts plated with chromium generally last significantly longer than those plated with substitute coatings (ref. 304). Over time, this reduces the total number of parts that needs to be processed and further reduces the quantity of waste generated.
EPA recognizes the importance of considering all inputs and outputs in manufacturing and recommends a process termed life-cycle assessment to objectively identify and evaluate opportunities to reduce the environmental impacts associated with a specific product, process or activity. Life-cycle assessments take a holistic approach by analyzing the pollutant quantities and environmental impacts associated with: extraction and processing of raw materials, manufacturing, transportation, distribution, use/reuse/maintenance, recycling and final disposal (ref. 302). The life-cycle process should be kept in mind when reading this section, especially with regard to alternatives to cyanide, cadmium and chromium.
6.2 PRODUCT CHANGES
EPA defines product changes for pollution prevention purposes as: changes in the composition or use of the intermediate or end products performed by the manufacturer with the purpose of reducing waste from manufacture, use, or ultimate disposal of the products (ref. 302).
The responsibility of product changes falls mostly on the manufacturer because they have control over the design and specification of the product. Unfortunately, when products and product components are processed by subcontractors, such as electroplating job shops, the effects of poor designs are felt by others. As discussed in Section 2, the majority of plating shops surveyed during the NCMS project were job shops. Not surprisingly, most of these shops either did not respond to the question of product changes or they indicated that this section of the survey was not applicable to them. This attitude is an important environmental disconnect between designers and platers which has been identified in several documents relating to environmental impacts of the electronics industry (ref. 518, 519). However, a number of job shops indicated that they do have some input on the design of the parts that they plate. In an effort to convey the actual attitudes of the respondents, actual responses to the product changes question are printed in this section in their entirety. To differentiate between the responses provided by captive and job shops, the captive shop responses are printed in bold type (includes all shops that declared themselves 1% or more captive).
The responses are divided into two groups, negative and positive responses.
6.2.1 Negative Responses to Product Changes
- Our customers are rather disinterested in pollution prevention that they can employ (PS 039).
- N/A [not applicable]—We are a job shop (PS 055).
- N/A—We are a job shop and have no control over what the customer wants us to plate (PS 066).
- No control over parts—We are a job shop (PS 098).
- Because this company is a job shop we have no control over the design of the parts to be plated (PS 116).
- We are a job shop. The customer designs the part, therefore we have no control over product design. Some customers are cognizant of problems concerning plating, but the majority just tell us to plate it or they will take it elsewhere (PS 128).
- N/A-All product is customer supplied (PS 174).
- We don't manufacture parts (job shop) (PS 175).
- N/A—Contract only shop (PS 199).
- We are a job shop only. We rarely have input into a customer's designs to improve plating and reduce pollution
(PS 204).
- N/A—We are a job shop anodizer (PS 230).
- Products supplied by customers, no control (PS 233).
6.2.2 Positive Responses to Product Changes
- We have gotten customers to change their plating specification from brass or nickel-brass to "simulated
brass." This is zinc plating with a blue chromate dyed to a brass-tone. As a result, we have converted
50,000 lbs to 75,000 lbs [of parts] per month from cyanide-brass to acid zinc (PS 004).
- If drain holes are not present, we will not plate the parts. Usually the customer will add adequate holes with
no problem (PS 010).
- We have reviewed the design of parts in an effort to reduce dragout and contacted our customers with recommended
changes (e.g., use of easily cleaned material and change to non-petroleum machine lubricants) (PS 041).
- On proprietary furniture, we have optimized orientation and drain holes (PS 058).
- We insist on drain holes (PS 082).
- Redesign of racking and adding drain holes to reduce dragout (PS 089).
- Had customer redesign some weldments to avoid pockets that trap solution and added drain holes to other parts
(PS 099).
- At one time we copper plated bars used in the textile industry. Later, we would buy this material already
plated. Now, this product is manufactured from stainless steel and copper plating is not needed (PS 102).
- We request and usually get permission to drill additional drain holes in tubular products (PS 109)
- Whenever necessary, we ask our customers to include drain holes or change the design to improve drainage (PS
124).
- We work with customers to control the drainage of parts (PS 125).
- As a job shop we do not have much control on design changes, but there have been times when we were successful
in making suggestions to our customers where a change was possible (PS 156).
- We provide constant customer education for part modification and design. In some cases we refuse jobs involving
problem designs. Our success is difficult to determine since this is our business philosophy, but we feel we are
generally successful (PS 172).
- We communicate with customers on part design to include drain holes (PS 176).
- We refuse work that is highly oiled or soiled and return them to the customer for cleaning. We have the customer
provide adequate drain holes, and we recommend corrosion resistant parts when feasible (PS 188).
- We have implemented drain holes, material substitution and racking modifications (PS 192).
- Auto companies have changed part finish specifications to use processes perceived to reduce pollution problems
(PS 214).
- Provide input on part design, when possible (PS 228).
- Some customers have implemented changes to allow for adding additional drain holes and additional
"dimples" to separate barrel plated work (PS 245).
- We advise our customers on proper drainage in the design of their parts (PS 251).
- Redesigning of parts to add or re-position drain holes has been successful (PS 275).
- Successfully replaced hot rolled steel with cold rolled steel to reduce pickling (PS 288).
- We "no-quote" work that could generate excessive dragout. Tooling has been re-configured for more evenly distributed plating. Plastisol coating of tooling is increased to avoid stripping/plating of our racks (PS 298).
6.3 CHLORINATED SOLVENTS USE REDUCTION/ELIMINATION
Chlorinated solvents have been used extensively in the metal working and metal finishing industry for degreasing and cleaning. The most commonly used degreasing solvents include: 1,1,1-trichloroethane (or TCA), trichloroethylene (or TCE), perchloroethylene (or PERC), chlorofluorocarbons, (or solvent 113) and methylene chloride. These solvents are used in a variety of methods, but most frequently in vapor degreasers, immersion or spray operations, and hand wiping. Solvent use has declined during recent years and especially since 1990, due to regulations restricting the use of ozone-depleting substances, voluntary actions by industry under EPA's 33/50 Program (Industrial Toxics Project) (ref. 203), rising costs for the purchase of solvents and the disposal of solvent wastes, and concerns over the health effects of solvents. However, as late as 1989, an estimated 73,000 U.S. firms (includes all types of industry) still used vapor degreasing with TCA (ref. 79).
![]() |
![]() |
Solvent use among the respondents to the Users Survey is summarized in Exhibit 6-1. Column 1 indicates the shop code number (PS 001 to PS 318). Column 2 shows the type of solvent used. Column 3 indicates the percentage of the shop's work that is job shop-type. Where 100% is shown, that business is entirely a job shop. Where 0% is shown, that business is entirely a captive shop. Where a different percentage is shown, that shop does both job and captive-type work. Column 4 indicates the year that the business commenced plating operations. Column 5 indicates the year that solvent use was eliminated. Where no year is shown in column 5, the solvent process was still in use at the time of the survey. Columns 6 and 7 indicate the quantity of solvent (in gallons or pounds) that is currently used or was used in cases where the applications were eliminated. Column 8 indicates the type of application (vapor degreasing, cold dip, spray or hand wipe). The last column indicates the most sophisticated method that is used (or was used in the case of eliminated applications) for controlling solvent emissions. The following abbreviations are used (shown in increasing levels of sophistication):
NONE | no controls |
FREEBOARD | increased freeboard of degreaser |
ROLLTOP | automatic rolltop for degreaser |
LIFTSPEED | controls to limit vertical speed of degreaser hoist |
REFRIGER | refrigeration zone to supplement conventional cooling coils |
Exhibit 6-2 shows that among respondents to the Users Survey, the number of solvent users has changed since 1980. In Exhibit 6-2, the shops are divided into three groups: (1) those in existence in 1980; (2) those established from 1981 to 1985 (inclusive); and (3) those established from 1986 to 1993 (inclusive). For the older shops, the number of solvent users remained approximately the same from 1980 to 1985 and then declined substantially from 1986 to 1993. In 1980, 53% of the shops used solvent and by 1993 only 39% used solvent. Therefore, 26% of the solvent users in 1980 have eliminated its use. For shops established from 1981 to 1985, the frequency of solvent use was below that of the older shops in 1985 and then from 1986 to 1993, the percentage declined similarly to the declining use rate of the older shops. Thirty-one percent of the shops established from 1981 to 1985 that originally used solvent have eliminated its use. The most recently established shops (1986 to 1993) presently have approximately the same percentage of solvent use as the shops established in 1981 to 1985.
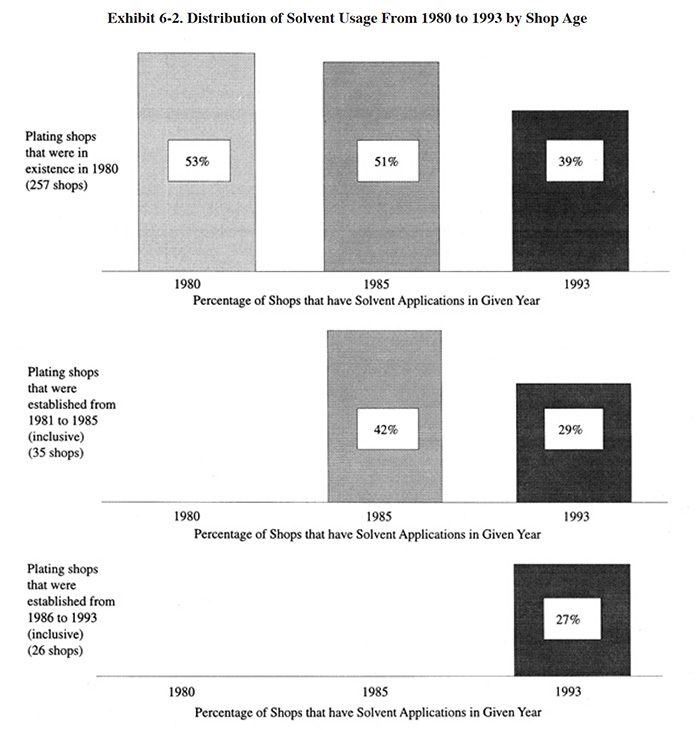
Exhibit 6-2 indicates that shop age had only a small bearing on the frequency of solvent use. This is somewhat surprising since older shops are often thought of as being less likely to change their operational procedures and processes.
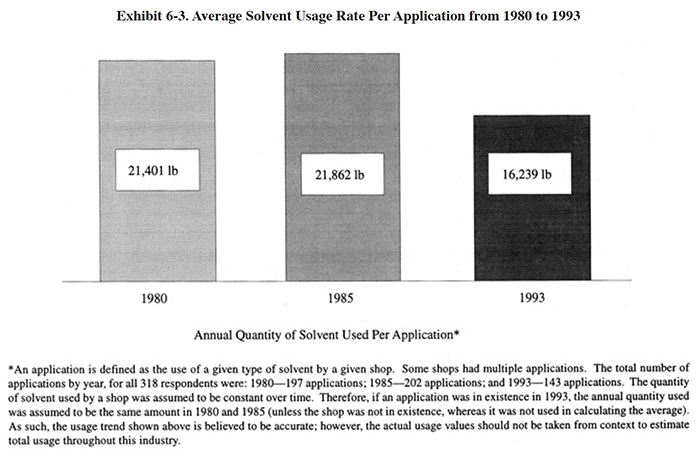
Exhibit 6-3 shows that the quantity of solvent use per application has also declined during the time period 1980 to 1993 and that this decline has been restricted to the time period of 1986 to 1993. A solvent application is defined as the use of a given type solvent by a given shop. Therefore, shops can have more than one solvent application. Combined with the fact that there are fewer applications, overall solvent use has declined significantly, probably by 50 percent or more from 1986 to 1993. All of the solvent use data are contained in the database and users are encouraged to utilize the database and draw their own conclusions.
Solvent use reduction has been achieved by survey respondents by improving the designs of vapor degreasers and the operating practices used with these units and by substituting aqueous and semi-aqueous cleaners for solvent degreasing. The most frequent vapor degreaser design and operating changes made by survey respondents focus on reducing solvent emissions, and include: increasing freeboard, adding a rolltop, controlling hoist speed and adding a refrigeration zone (see Exhibit 6-1). Of the 90 vapor degreasing applications in use in 1993, at least 75 percent were equipped with one or more of these design and operational changes. Various substitutions for solvent have been made by the survey respondents and these are discussed later in this section.
Although the numerical survey data provide insight to the changes regarding solvent use in the metal finishing industry, the comments submitted by respondents give an even clearer picture. The remainder of this subsection is devoted to their comments.
Sixty-eight percent of the respondents that are presently using solvent identified that its elimination is a pressing environmental problem. These shops are at various stages in the process of elimination. Some shops indicated that they are just beginning to evaluate solvent substitution alternatives (PS 156, PS 165, PS 184) and other shops indicated that they have made progress and are continuing to work toward elimination (PS 124, PS 166, PS 176, PS 178, PS 181, PS 191). Only 11.7 percent of the solvent users gave an indication that they plan to continue the use of solvent. These shops gave a range of reasons why solvent use is necessary. These reasons include:
- Solvent use is necessary to meet aerospace requirements (PS 121).
- Unsuccessful at attempts to clean zinc die castings without solvent (PS 089).
- Solvent is needed to remove polishing or buffing compounds (PS 098, PS 170, PS 171, PS 191, PS 205).
- No single answer for replacing solvent degreasing (PS 049).
- Some non-solvent products work well, but there is always a problem with long drying times for parts.
- Have replaced TCA vapor degreasing with alkaline cleaning, but can't replace acetone used to strip maskant (PS
166).
- Substitutes are too expensive (PS 217).
- Citrus cleaners did not work (PS 248).
- Tried six different safety solvents (citric based). None were satisfactory due to residue or unacceptable evaporation time (PS 271).
A number of problems with solvent substitution were cited by survey respondents. These include the following comments from both successful and unsuccessful substitution efforts:
- Alkaline cleaners increase the amount of waste treatment performed and/or the labor for these efforts (PS
114).
- More difficult to remove masking wax without solvent (PS 108).
- Citric acid based emulsion cleaner leaves a residue that inhibits good plating and causes poor adhesion (PS 109,
PS 271).
- "Orange-Peel Cleaners" caused skin rashes on employees and excessive foaming in the waste treatment
system (PS 021).
- Caused oil fouling of ion exchange resins (PS 130).
- Increased labor for degreasing and/or bath maintenance (PS 130, PS 262).
- Created a new wastestream (e.g., oily waste, spent cleaner) in some cases that is more difficult to deal with
than solvent waste (PS 153, PS 171).
- Solvent substitutes simply do not perform as well as solvents (PS 163).
- Substitutes are too expensive (PS 217).
- Citrus smell of substitute cleaners is objectionable.
- Many substitutes contain chelating agents or surfactants that interfere with metal hydroxide precipitation (PS
296).
- PS 021 indicated that they had a "difficult transition" that took approximately 24 months and "a lot of patience." Their efforts included trials with terpene cleaners, "terpene-like cleaners and non-ionic surfactant packages," and finally they settled on a mildly alkaline aqueous cleaner with a non-ionic surfactant. They also use barium carbonate for post cleaning but eventually switched to pumice. These changes combined with "enough (cleaning) time" and "elbow grease" have resulted in "few cleaning problems."
Only two shops specifically indicated that there were no production related problems associated with the substitution for solvent degreasers (PS 153, PS 190).
Some respondents provided information with regard to successful substitute degreasers that they use in place of chlorinated solvents. The following responses were given:
- Aqueous cleaner with glycol ether (PS 064).
- Aqueous cleaner (PS 124, PS 166, PS 187, PS 292, PS 268).
- Citri-Solv product and Safety Clean (PS 105).
- Mildly alkaline, biodegradable aqueous cleaner with a non-ionic surfactant (PS 021).
- Global 6 (PS 169).
- Aqueous, citric, terpene cleaners (PS 174).
- Emulsion cleaner (PS 181).
- Alkaline power washer (PS 079, PS 197).
- Alkaline non-etch ultrasonic clean, Enthone NS-35 (PS 221).
- Increased concentration of existing cleaner (PS 253, PS 295), e.g., PS 295 eliminated solvent use (80,030 gal/yr
CFC 113 and TCA) by increasing cleaner concentration from 10 oz/gal to 12 oz/gal.
- Converted degreasers to soak cleaners and use 7-9 oz/gal Midstate 4310, 140 - 180 oF, alkalinity ratio 0.40
minimum, soil load 10% maximum (PS 273).
- Water soluble solvents (PS 276).
A number of miscellaneous methods were employed to reduce solvent use; these include:
- Use safety solvent cans with hand wipe operation (PS 069, PS 176).
- Use low vapor pressure solvent blend in place of MEK for hand wiping.
- Increase level of training and reviewed good operating practices in safety meetings (PS 191).
- Increased use of hand wiping and decreased use of vapor degreaser (PS 191).
- Added inspection of degreaser to regular monthly procedures (PS 191).
- Working with customer on the cleanliness of parts (PS 248).
- Increased agitation in cleaning bath.
- Subcontract the 5% of workload that requires solvent degreasing.
- Install solvent recovery stills (PS 124, PS 149).
6.4 CYANIDE USE REDUCTION/ELIMINATION
Cyanide, in the form of either sodium or potassium cyanide, has been a key component of plating solutions for many years. Some of the metals commonly plated from cyanide baths include: cadmium, zinc, copper, brass and precious metals. When used, cyanide forms a moderately stable complex with metal ions that permits the deposition of the metal under the influence of a suitable electrical potential.
Although cyanide-containing baths are eminently satisfactory as far as plating results go, pollution control poses a problem in terms of both compliance and economics (ref. 350). As a result, there has been a significant effort to find and implement cyanide-free plating processes since approximately 1975.
Survey respondents indicated concerns over the use and control of cyanide and expressed a desire to find alternative non-cyanide plating solutions. For example, 14 percent indicated that they currently have compliance difficulties with cyanide. Eleven percent indicated that improved cyanide plating alternatives or controls was a major environmental technology need for their company. Twenty-six percent of the respondents indicated that there exists a technology transfer insufficiency with respect to non-cyanide finishing. This was the highest percentage of response for any topic listed in the survey form (see summary of results in Section 2).
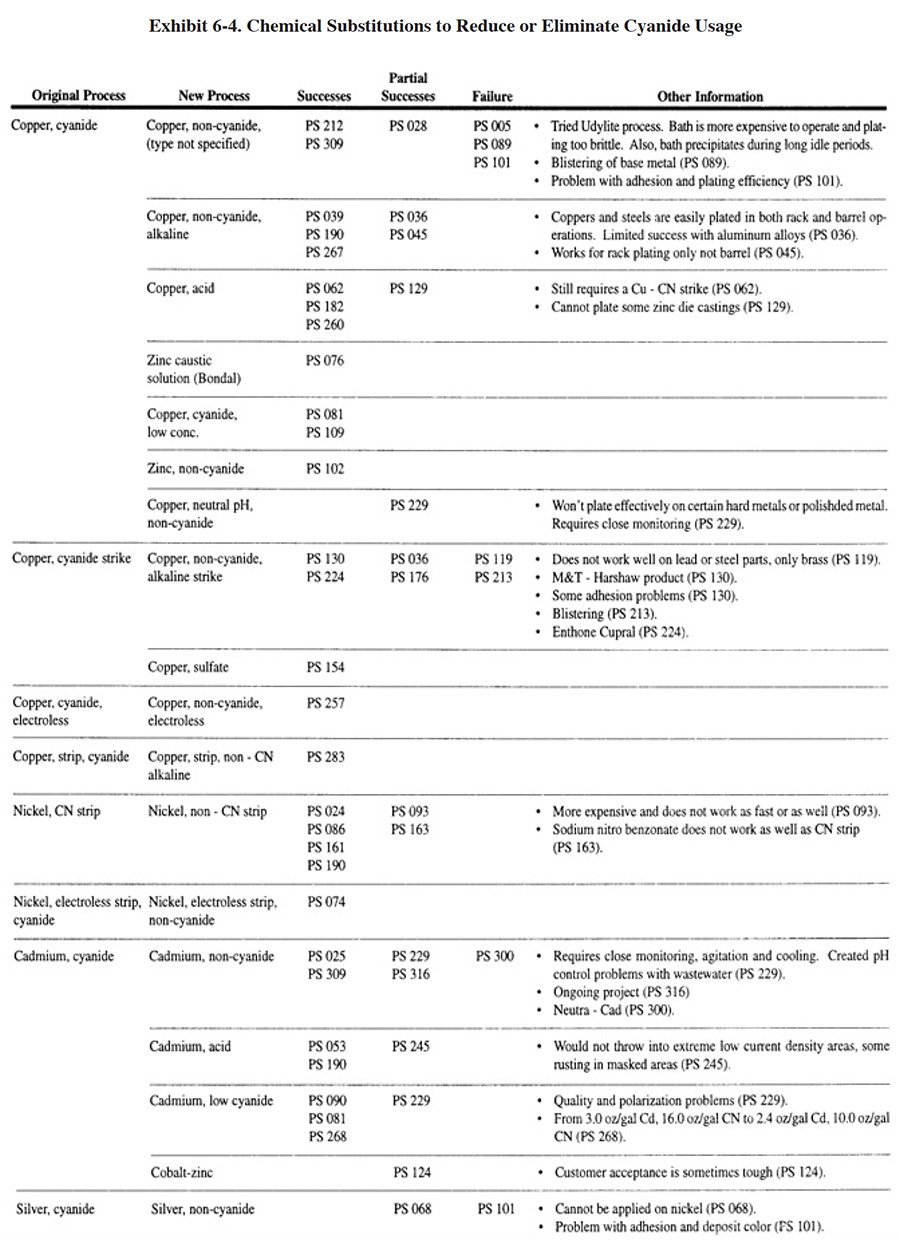
The earliest and most complete cyanide substitution that has taken place in the plating industry is the conversion from zinc cyanide plating to zinc chloride and zinc alkaline (non-cyanide) plating. Although some respondents indicated that they did not make this substitution until the 1990's, most respondents converted during the period of the late 1970's to mid-1980's. A total of 28 respondents (or approximately 17% of the zinc platers) successfully converted to zinc chloride, 18 respondents (or approximately 11% of the zinc platers) converted to zinc alkaline (non-cyanide) and 8 respondents (or approximately 5% of the zinc platers) converted to an unspecified zinc non-cyanide plating process (see Exhibit 6-4). Another 9 (or approximately 6% of the zinc platers) converted from a high cyanide to a low cyanide concentration bath. Perhaps even more impressive than the number of successful conversions is that only 2 respondents of all those that attempted conversions were unable to successfully make a substitution.
One significant drawback with regard to zinc cyanide plating substitution is that some shops found it necessary to install both zinc chloride and zinc alkaline (non-cyanide) baths to replace the single cyanide bath (PS 053, PS 059, PS 087, PS 204, PS 251, PS 288, PS 300). On a positive note, in addition to cyanide use reduction, some platers enjoyed production benefits from the substitution, including better and brighter plating.
In addition to zinc plating, a significant number of respondents have reduced or eliminated cyanide usage with copper plating and nickel stripping, although the success rates (i.e., ratios of successes to attempts) are not as high as for zinc plating. Other plating and finishing cyanide solutions for which substitutes were identified by respondents included cadmium, silver and brass plating and chromate conversion coatings. The number of successes was either limited or non-existent for these solutions.
In addition to the plating shops that indicated they have substituted a non-cyanide process for a cyanide process, there were 12 shops that simply eliminated approximately 22 cyanide plating processes in order to meet environmental regulations.
6.5 CADMIUM USE REDUCTION/ELIMINATION
Cadmium, which is most often plated from a cyanide solution, was identified by the respondents of the Users Survey to be of significant concern. At the time of the survey, 30 percent of the respondents performed cadmium plating using a cyanide bath and 2 percent used a non-cyanide bath. Ten percent of all respondents indicated that they have compliance difficulty with cadmium. Seventeen percent indicated that they felt there was a technology transfer insufficiency with respect to cadmium and 8 percent indicated that there was a need for better cadmium alternatives or control technologies.
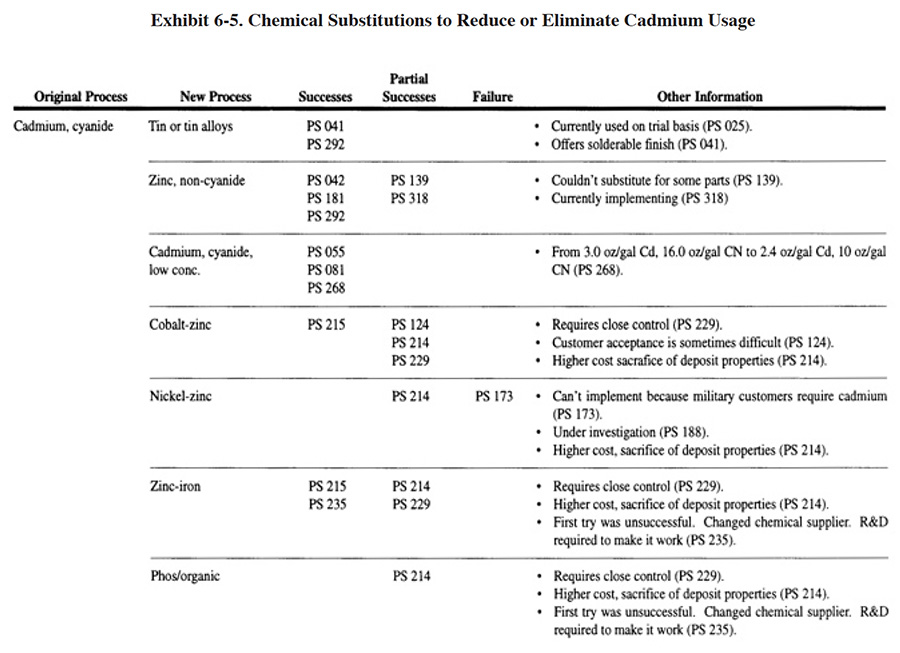
Based on the results of the Users Survey, it is obvious that cadmium-cyanide plating is much more difficult to substitute for than cyanide-based plating in general (see Exhibit 6-5). Only 8 of the respondents (or approximately 8% of the cadmium platers) have successfully made this substitution, with another 8 (or approximately 8% of the cadmium platers) indicating partial success. Another 3 respondents (or approximately 3% of the cadmium platers) have successfully implemented a low-cyanide, low-cadmium substitute. No single cadmium substitute stood out as the most successful, with tin and tin alloys, zinc (non-cyanide), cobalt-zinc and zinc-iron being used. The primary problems with cadmium substitutes were: (1) customer acceptance; (2) the quality of the finish; and (3) their higher cost.
In addition to the plating shops that indicated they have substituted non-cadmium or low-cadmium processes for a conventional cadmium process, there were ten shops that indicated they have eliminated cadmium plating in order to meet environmental regulations.
6.6 CHROMIUM USE REDUCTION/ELIMINATION
Chromium is heavily used in electroplating and aluminum finishing. The most common chromium bearing solutions include: decorative and hard chromium, aluminum conversion coating, bright dipping of copper and copper alloys, chromic acid anodizing, deox/desmut and chromium stripping (see Section 2 for data on the use of each of these processes). Due to its high toxicity and the cost for treatment and disposal of chromium bearing wastes, it has been a target for reduced usage or elimination.
The results of the Users Survey indicate that 18 percent of the respondents have compliance difficulty with chromium. Twenty percent of the respondents indicated that there exists a technology transfer insufficiency with regard to non-chromium metal finishing.
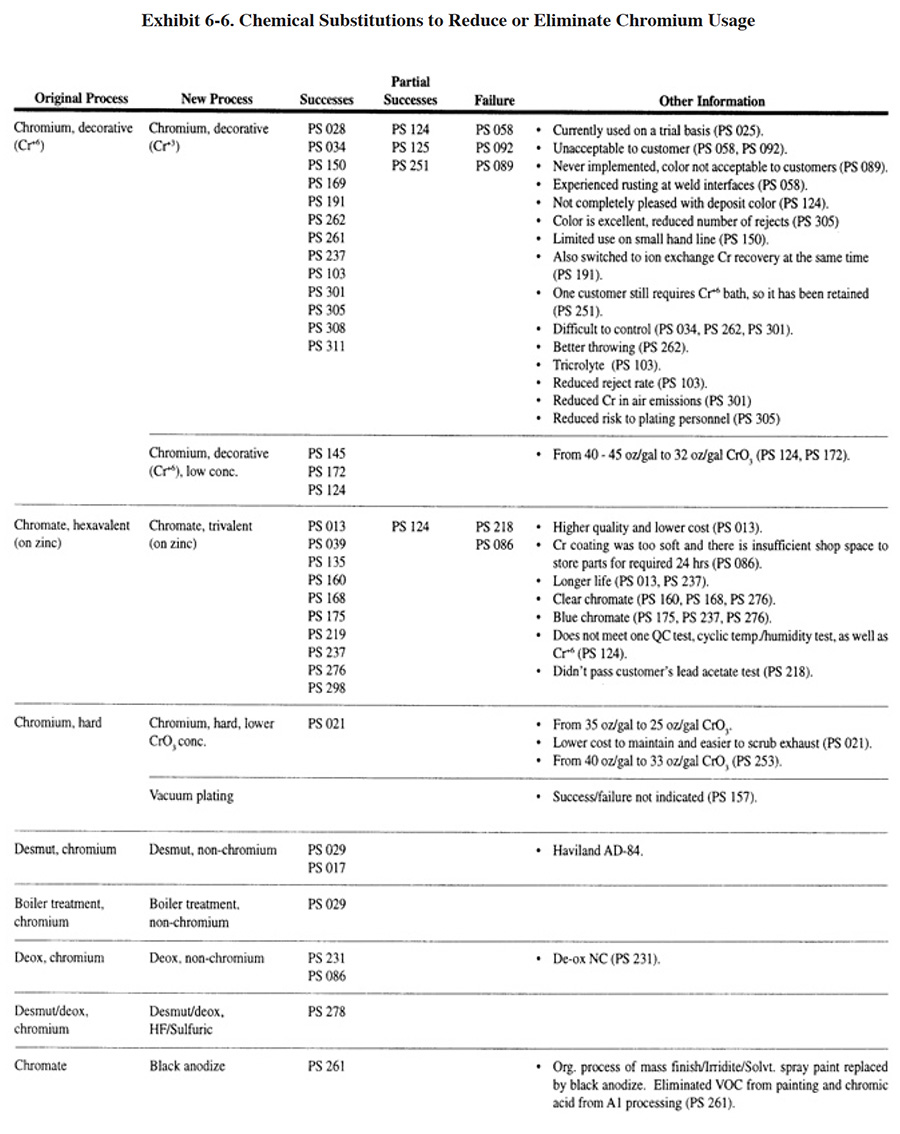
Efforts to reduce chromium usage in the aerospace industry and for military applications have focused on non-chromium aluminum finishing and hard chromium plating substitution (ref. 75, 77, 211, 418). However, among survey respondents, which are mostly job shops, efforts were directed more at substituting trivalent chromium decorative plating and zinc conversion coating solutions for the traditional hexavalent baths. Both of these substitutes offer cost savings in terms of lower wastewater treatment chemical usage since the hexavalent chromium reduction step is eliminated. Also, trivalent chromium plating solutions are formulated with as little as 6 g/l of chromium, significantly less than their hexavalent counterparts (ref. 89). The lower chromium concentration in the baths results in less chromium in the dragout. The substitution of trivalent plating solutions was generally successful for the survey respondents (15 shops), although some exceptions were identified (see Exhibit 6-6). Sixty percent of these respondents indicated that the process substitution was successful, 20 percent indicated it was partially successful and 20 percent indicated that their substitution efforts failed. The most frequent problem with the process was its acceptability to the shop's customers; a problem that was primarily related to the color of the deposit.
Switching from a hexavalent chromium zinc conversion coating (both clear and blue) to a trivalent coating was successful in most cases. Seventy-six percent of the shops attempting this substitution were successful. Another 8 percent were partially successful and only 15 percent resulted in failure. The limited success of one respondent and the failures of others were related to the characteristics of the coating.
In addition to the plating shops that indicated they have substituted a non-chromium, trivalent chromium or low-chromium process for a conventional chromium process, there were four shops that simply eliminated chromium plating and one shop that eliminated chromating of magnesium in order to meet environmental regulations.
6.7 OTHER CHEMICAL SUBSTITUTIONS
Substitutions made for environmental reasons, not involving the previously discussed four Cs chemicals, are shown in Exhibit 6-7. These other substitutions were implemented for two main purposes: (1) to reduce the mass of metal or other undesirable constituents in the wastewater and (2) to improve the performance of their treatment operations by reducing the use of chelating compounds. As indicated in Exhibit 6-7 nearly all of these substitutions were successful.
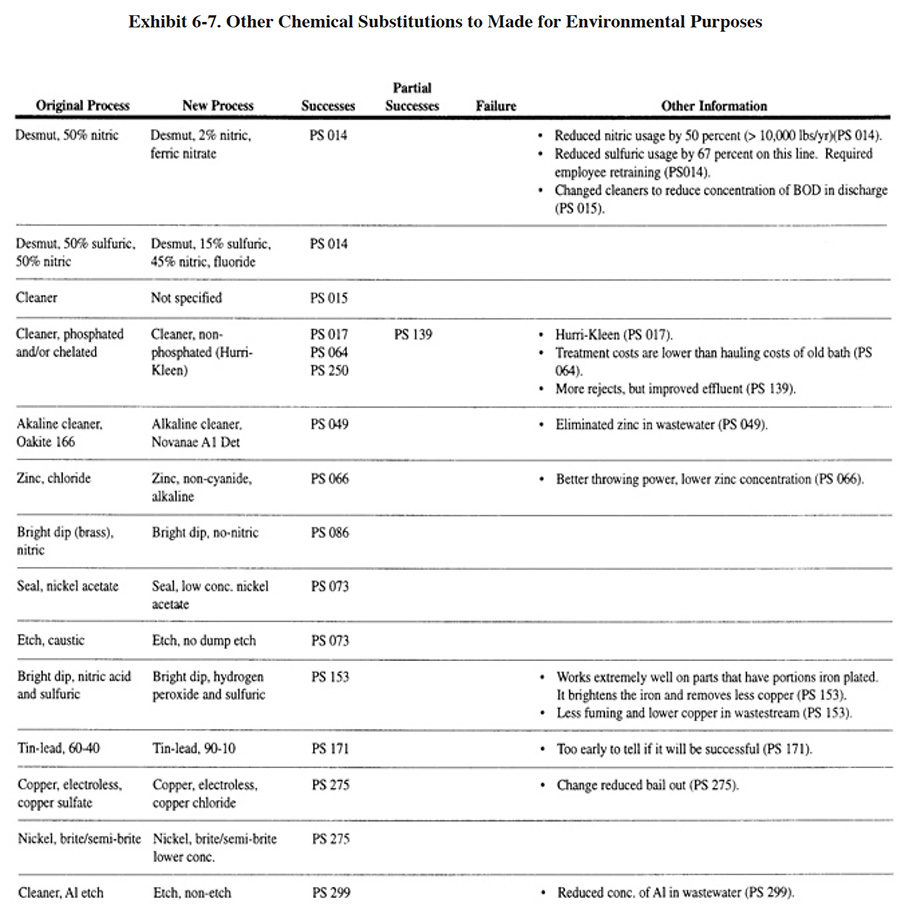